Tips for Decreasing Points of Failure in Motor Systems Design
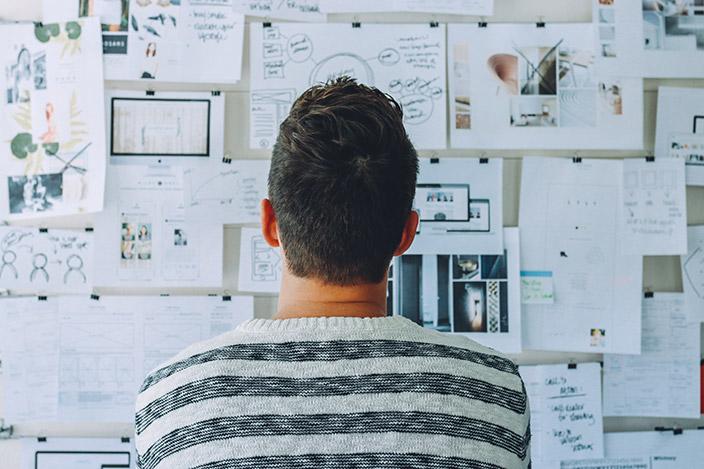
Tips for Decreasing Points of Failure in Motor Systems Design
Engineers are constantly tasked with providing the right solution for an application while maintaining specifications that lead to long life, while also under strict budgetary concerns. Passing decisions along to the purchasing department where costs might outweigh quality, inexpensive parts bought for every component needed throughout the design can quickly turn into a disaster. Knowing which components are critical will help engineers focus on those devices that will strengthen their design without breaking their banks.
Moving Components
The way to keep overall costs down throughout the entire design, manufacturing, and maintenance cycle is to focus early in the design phase on those components that provide the required motion your application requires. This approach is the most forward-thinking, in that it is meant to reduce the maintenance and support functions that come down the line in the event that you’ve skimped on quality motion components. Remember, you can purchase low-cost components early on, but then pay later with machine breakdowns. Focus prototype and design time on the quality of moving components and you’ll strengthen your system’s ability to operate over an extended life cycle.
Through designing for manufacturing, it’s not just component costs that are concerning but mounting methods and orientation. Orientation particularly has a dynamic effect on which motion components you will select. A cantilevered motion system also poses unique stresses on motion systems. Design engineers often have a choice as to how they mount linear and rotary devices and should choose methods where motors and slides are not lifting their own weight as well as the load.
In an effort to provide quality, many motion engineers will over-engineer a system with motors that are larger than necessary, with extra sturdy rails or guides, or special mounting designs that are not necessary. Literally, any over-engineering infuses a system with additional components or components that must over-compensate for design flaws, often incorporating more opportunity for failure.
Proper design means selecting high-quality components that contribute to the most critical parts of your system, providing value rather than complexity. Cost-cutting when it comes to moving components tends to decrease the quality of the overall system by multiples. Inexpensive motion components particularly often integrate cheaper bearings, slide materials, or motor designs, which results in multiple places where one deteriorating part will have an adverse effect on every other part in the system.
Conformity Over Multiple Components
It isn’t merely part quality selection that counts. Choosing the right combination of products to address particular application needs is also an important issue. When ordering a variety of parts from different manufacturers to combine for your motion system, you are not taking into account the wide variety of manufacturing capabilities and quality checks that go into each component.
Different manufacturers use different machines to build parts. They also build their parts using different specifications and machine tolerances. These contrasting methods not only affect the quality of the individual part but have an even greater effect when parts are interconnected to supply a system. Mismatched components can be put together without awareness until the system struggles to react as the engineer expected. Optimized products based on specific application needs are more likely to come from one manufacturer than many.
The goal is to work with a manufacturer with a wide spectrum of capabilities. Expertise in motion control is key, but the breadth of products having optimal system performance when tied together is also important.
The Right Partner
Having many years in a particular market is key to understanding the motion system needs for a wide variety of applications. Companies that have been helping customers design and customize motion systems for years have the expertise a motion engineer might need for their next project. Even in-house design engineers have gaps in their knowledge base. It could be in optimized motor design, linear slide design, or in the required standards needed for a particular application, such as for packaging, food and beverage, medical, or aerospace design.
Getting quality assistance in customizing your needs to fit every requirement of your application is often based on what partner you decide to work with. You’ll want a partner that offers more experience than merely in moving parts, but also for selecting the right housings, shafts, wiring, connectors, and finishes. Ultimately, you want every step, from design to prototyping and testing, and from manufacturing to field operations, to go as smoothly as possible. Working with the right partner can do that.
Scaled Volume Delivery
One of the major failures companies experience when trying to deliver finished systems, is volume. Selecting and buying products then putting them together with the trust that they’ll work properly is only part of the concern of most systems designers. The other concern is ramping up part-deliveries when sales increase or a large order comes in. This is where working with multiple companies becomes a headache again. Not only is it time-consuming and costly to stay organized when purchasing from multiple vendors, but you are also strapped with inconsistent delivery times. Working with one company saves time, but only if they can quickly turn around large orders when needed. While researching part manufacturers, always double-check to be sure they can deliver when your volume unexpectedly increases.
Focusing on the potential failure points we’ve talked about in this article will allow motion engineers to reduce overall development costs, reduce time to market, and reduce overall system production, maintenance, and repair down the line. By working with a company that provides documented quality control ensures that you’ll get the consistency of the product with minimal specification drift across every component over time. This means that whether you need small, medium, or large-scale manufacturing, quality is maintained.
For more information:
News
Continue Reading
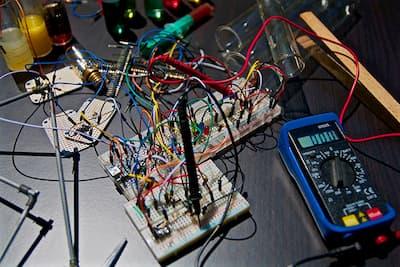
Solutions to Eliminate the Over-Engineering of Motion Control Systems
In today’s motion control market, space, cost, and specifications battle it out to produce a product that can compete in a growing marketplace without failing early. One of the issues includes over-engineering based on the fact that engineers need to be sure that their project operates the way it needs to from the starting gate.
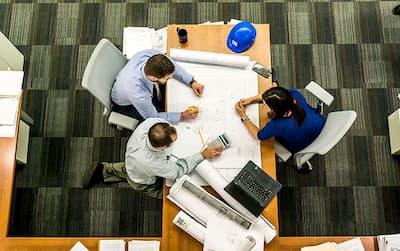
Motor Product Manufacturer, Engineering Consultant, or Both
Motor technology is getting more complex and more nuanced than ever before. This trend has made it extremely difficult for engineers to understand exactly what they may need for a particular application.