Miniature Linear Actuator with LinFinity Nut
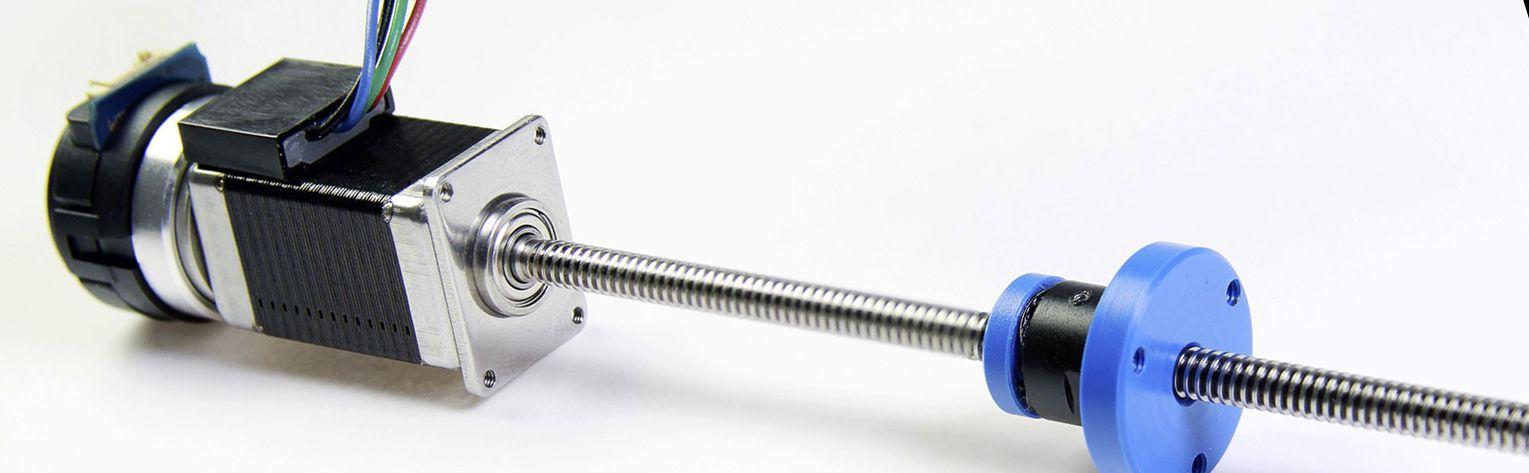
A Big Problem That Required a Tiny Solution
A customer reached out to us with a big problem that only a tiny motor could solve. They were looking to squeeze in a motorized linear actuator into a space that could not accommodate a conventional off-the-shelf type solution. On top of that, the actuator also needed to accurately move a 2lb (0.9kg) load with high accuracy, provide a feedback to the system, and also provide a maintenance-free performance. "Mission impossible", they thought. Well, for most Engineers and Suppliers, this challenge may have been impossible. But not for us! We knew that our new 106 motor was an ideal candidate to get the job done. Our Engineering team got to work prototyping an actuator system using the 106 motor that will get the job done. With a bit of tinkering, we’ve paired the motor with a lead screw to provide the right accuracy, added our self-lubricating LinFinity nut to remove backlash and provide maintenance-free performance, and also sourced an encoder that’s just the right size to provide the feedback the system needed.
106 Series Motor
The Smallest Hybrid Stepper
Most Engineers would look into Permanent Magnet (PM) Steppers for this type of project, as PM Steppers provide small enough foot print. However, the performance capabilities of a PM motor of this size wold not provide the needed torque at speed, or the resolutions needed for this particular project. Our new 106 Series Hybrid Stepper Motor measures just 16mm in width, making it one of the smallest Hybrid Stepper Motors on the market today, and the perfect motor for the job. The NEMA 6 frame size means that the 106 Hybrid Stepper Motor can be designed into challenging spots with minimal allotted space. Also, by increasing the step angle from a typical 1.8 degree to 3.46 degree, we were able to achieve nearly twice as much holding torque than a similarly sized motor with a standard 1.8 degree step angle.
This is perfect, as this particular project required a motor capable of higher speeds and torque than what a similarly sized PM Stepper could provide. The 106 motor delivers nearly four times more holding torque than a conventional permanent magnet (PM) stepper motor of similar size (which usually top-out at only 0.5 oz-in of holding torque), and can deliver similar speed performance of a BLDC motor. By combining the 3.46 degree step angle with our low inertia rotor design, we are able to achieve over 1 oz-in of dynamic torque at 8000 RPM. For this particular project, we’ve needed just a fraction of that speed.
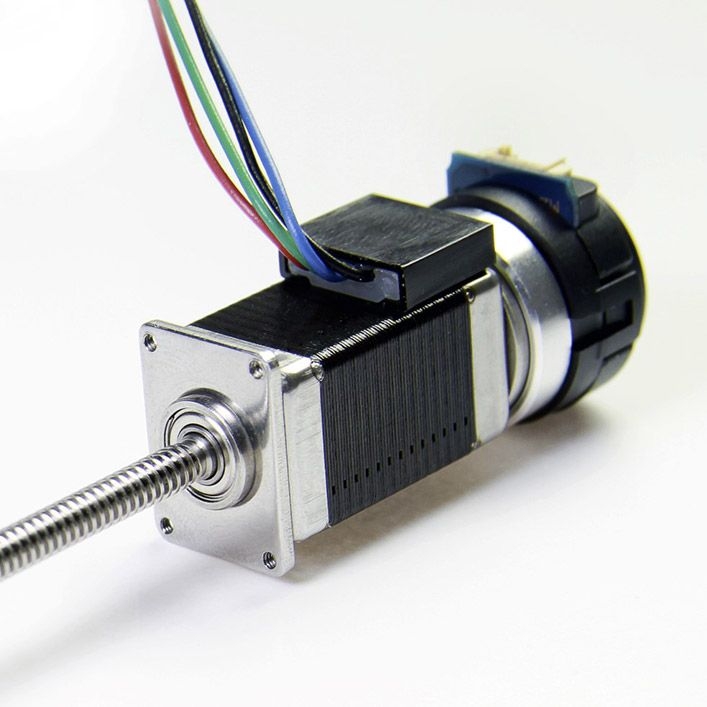
Linear Actuator System
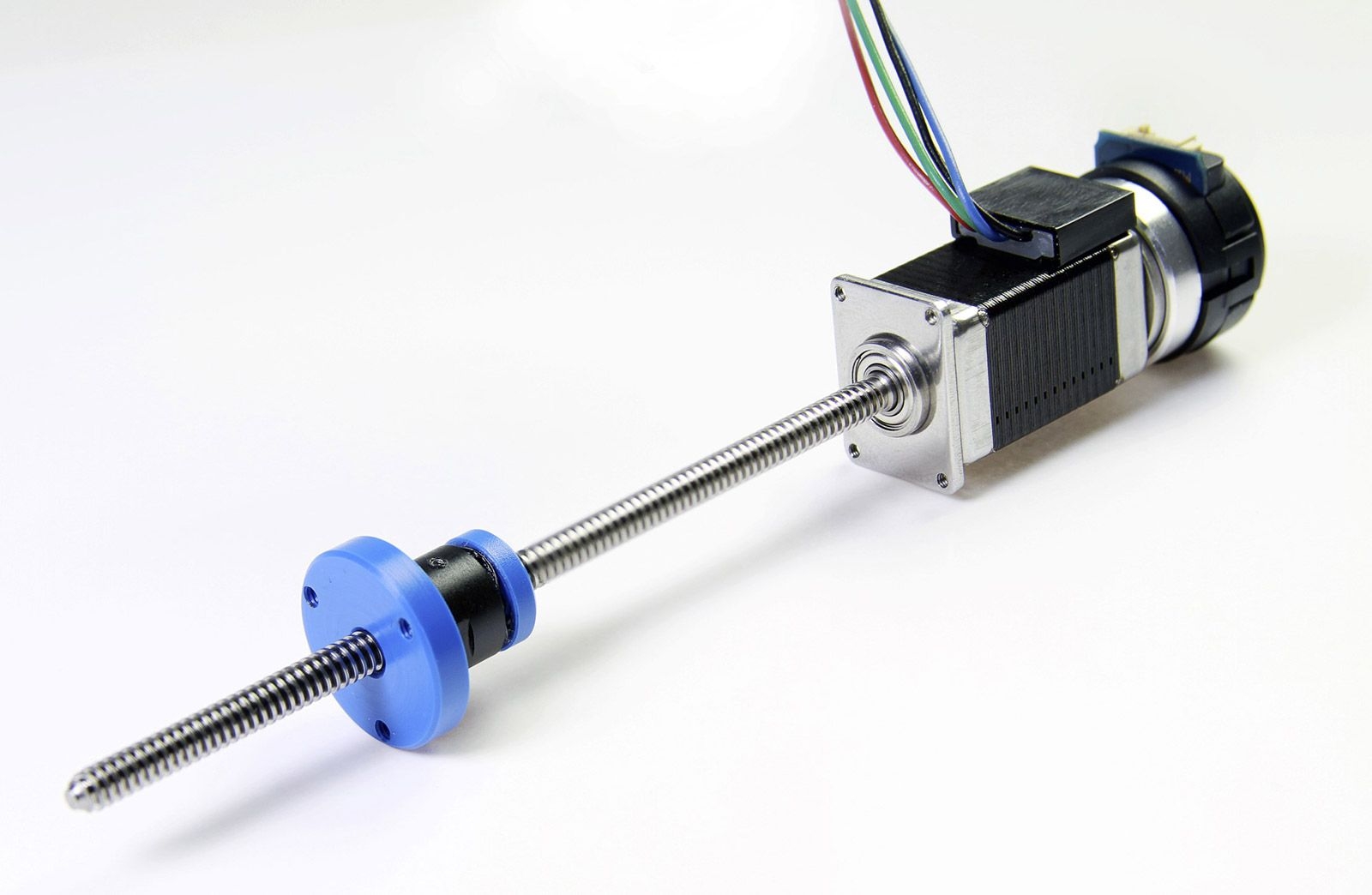
Because the 106 motor delivers more dynamic torque and high resolution than, we can utilize a higher efficiency lead screw while maintaining suitable force and accuracy. For this project, we’ve paired the motor with a screw with a 1 mm lead. The actuator is capable of delivering 2.5lb (1.1kg) of vertical force with the anti-backlash nut set to the appropriate pre-load. Of course, higher force could be achieved with a use of higher efficiency free-wheeling nut, without pre-load. But, in this case, accuracy was more important than higher efficiency. And since the actuator delivers sufficient force with plenty of margin for safety, we can be confident with the LinFinity anti-backlash nut choice.
Linfinity Nut
Maintenance-Free Performance
The LinFinity Nut is an internally lubricated anti-backlash nut. Our patented design incorporates an internal grease reservoir which distributes a consistent layer of grease throughout the entire surface of the lead screw as the nut travels. The internal reservoir maintains hydrodynamic lubrication throughout the life of the product, which drastically reduces friction and thus increases the performance and longevity of the product. For this particular project, these benefits are essential, as the system was designed to be sealed and therefore not readily available for regular maintenance or service.
Using a regular anti-backlash nut would not work in this situation. Ordinary externally lubricated anti-backlash nuts act as a wiper: instead of distributing the grease evenly, they tend to push the grease out to the edges of the screw. This results in the grease drying out and ultimately leads to product failure due to increased friction and heat buildup. The LinFinity nut reduces heat buildup by 20% or more compared to the closest competing design by reducing the overall friction. Lower heat and reduced friction along with even distribution of grease result in the overall life of the Linear Actuator system to increase.
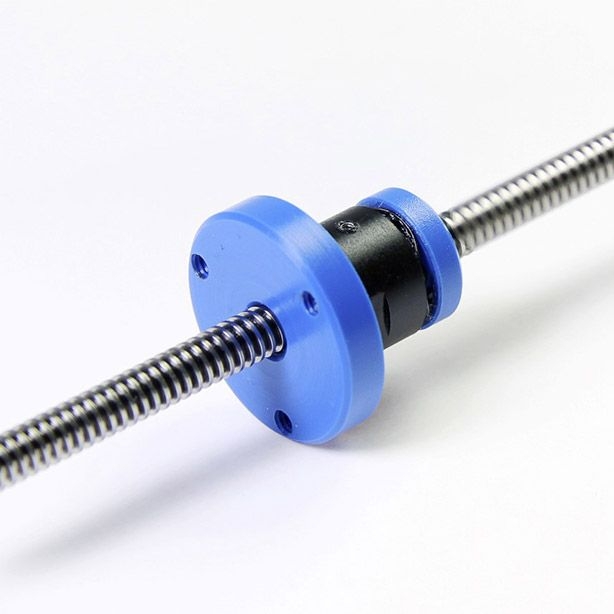
Miniature Encoder
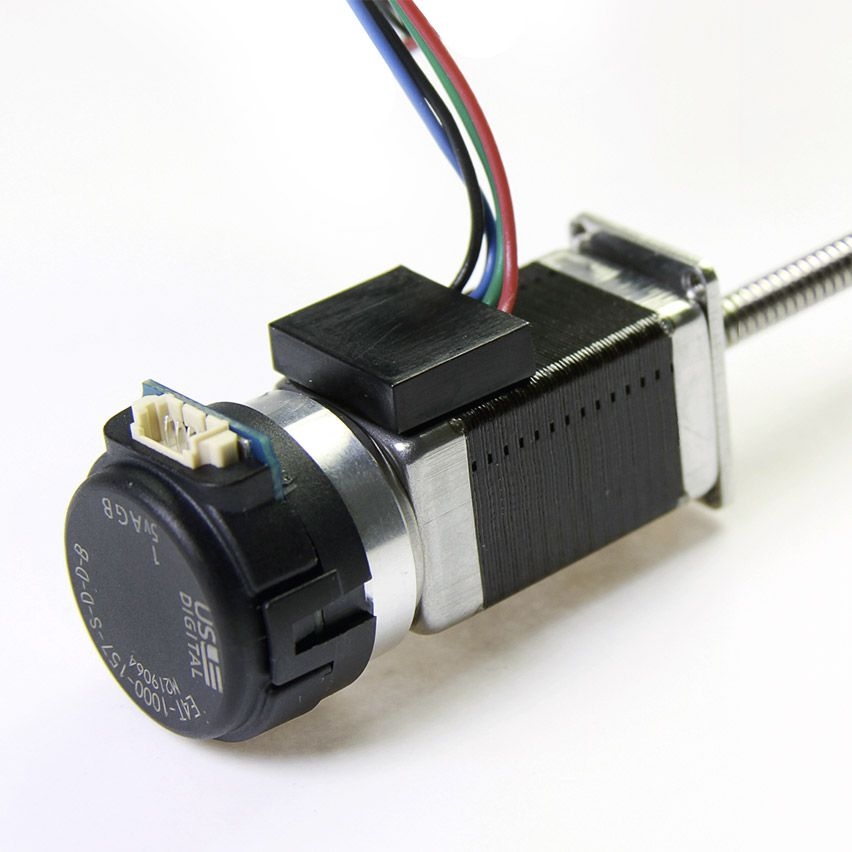
To provide the feedback to the system, We’ve equipped the 106 motor with a miniature transmissive optical encoder designed to provide digital quadrature encoder feedback and enables even higher precision by tracking precise movements. This encoder’s form factor is just right for this motor and the application constraints.
Result
The end result is that the customer got exactly what they needed. A small actuator, that will deliver the required performance, with minimal to no maintenance required. On top of that, we are able to support the customer through the lifecycle of their product. From developing a prototype, initial small batch, to full production runs.
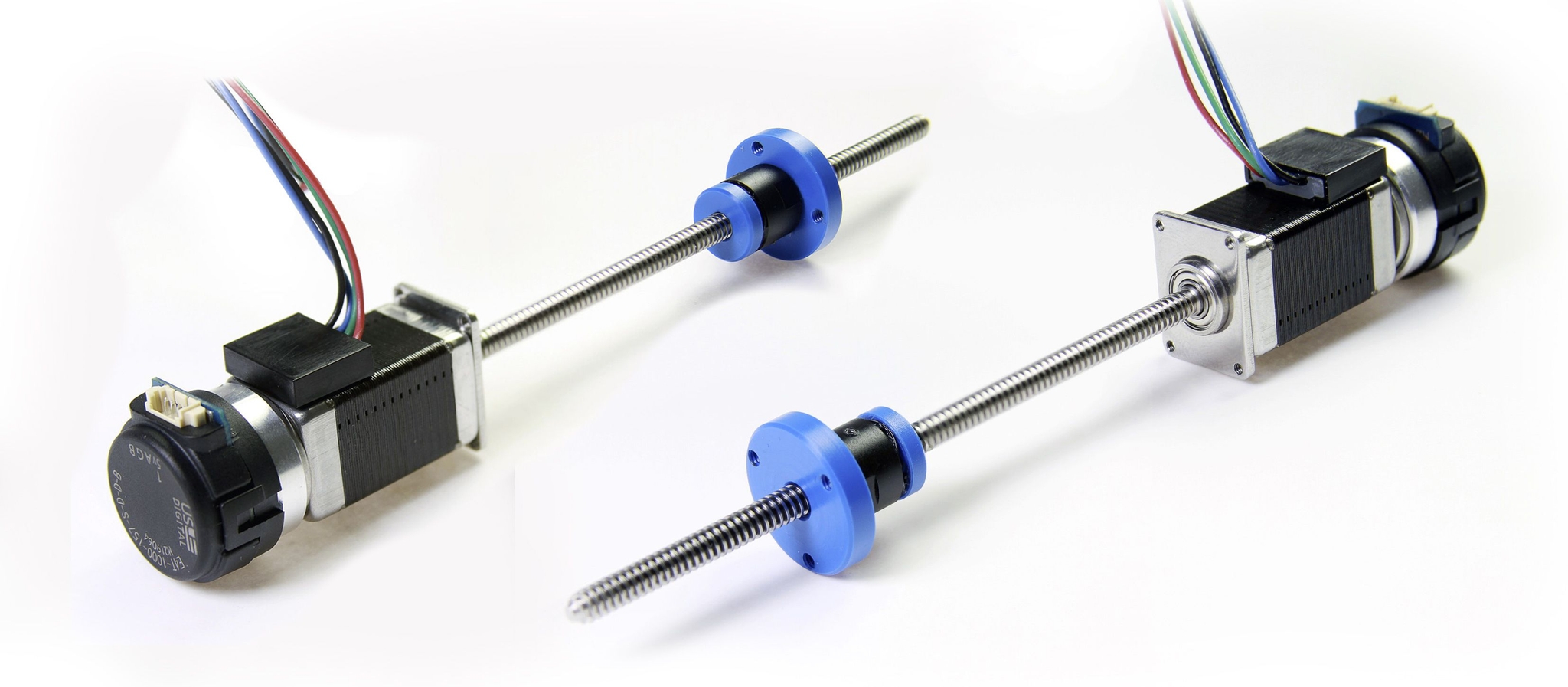
Learn more about how we can support you during your next product development project
Speak with one of our motion control experts about your next project.