3 Ways to Control Noise and Vibration in a Brushless Motor
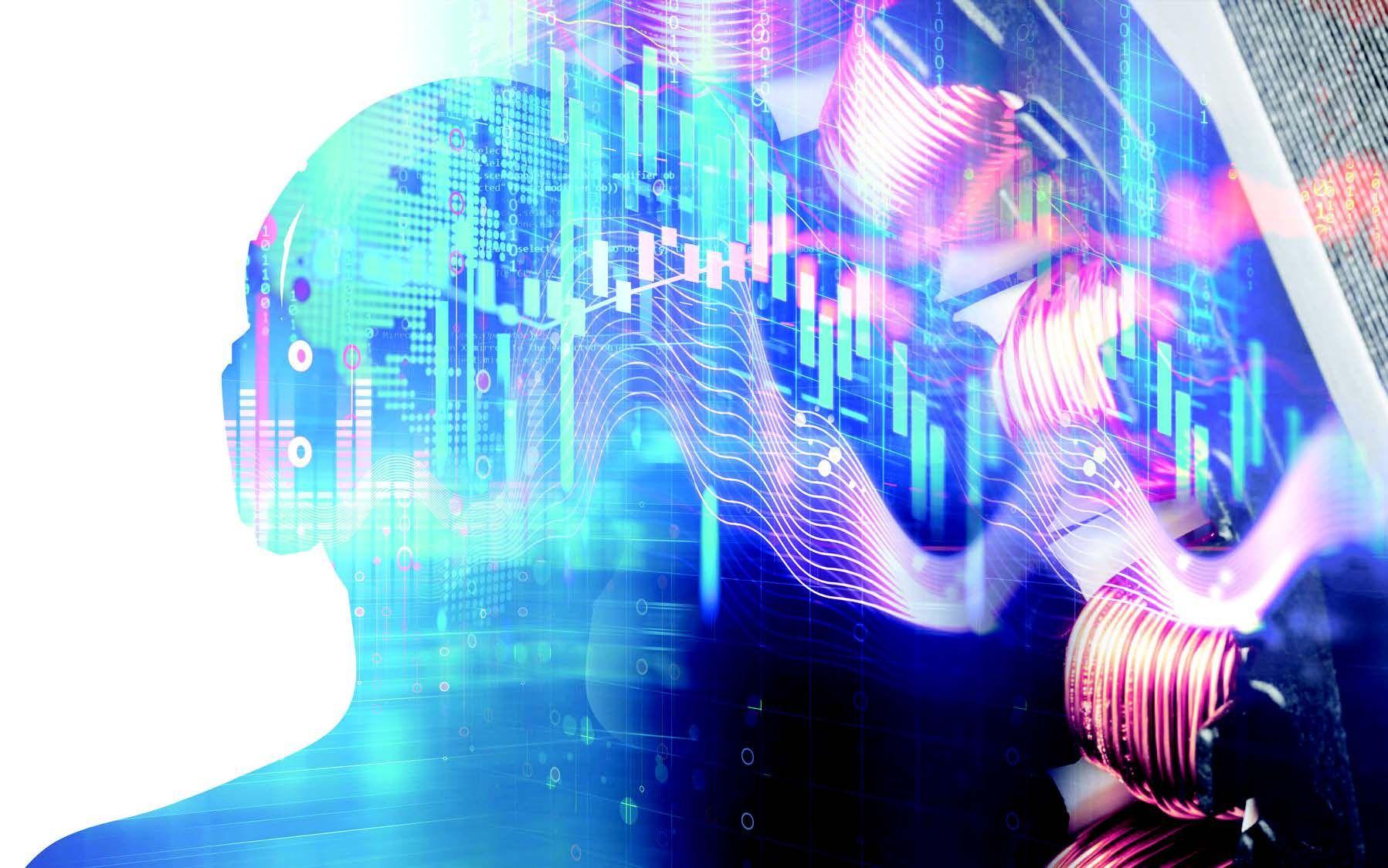
3 Ways to Control Noise and Vibration in a Brushless Motor
Uncontrolled noise and vibration can often cause a system to degrade quickly, affect efficiency, and adversely affect the overall wear and tear of a system. Understanding how to alleviate this problem, when it occurs inside your motor, can increase the life of your whole system.
Mechanical vibration and noise continue to be critical design factors when working with brushless DC motors. This is particularly the case with sensitive medical equipment, robotics, business systems, and handheld devices to name a few. Noise and vibration can have a substantial impact on system performance, reliability, and cost of operation. And for handheld devices, vibration can transfer to the user causing safety issues as well as stress injuries. For motors that operate around people, whether in hospitals, laboratories, or offices, excessive noise can make a device unacceptable for use in general.
Although system designers must continually understand their applications to be sure that they are aware of how load, mass, balance, and damping of other motion components are interacting, there is a lot that can be done within the motor as well. Brushless motors, with their permanent magnet rotor, were originally designed to operate more quietly than brushed motors as it is. Their design allows for the electrical winding to surround the stator rather than be on the rotor. In this way, the rotating mass is significantly lower and can be designed with greater symmetry, mitigating much of the vibration generated within the motor itself. Add to this design a few additional elements and noise and vibration can be reduced even further.
Bearing Selection
If the bearing system in your brushless DC motor is properly designed, it can last upwards of 25,000 hours. One of the primary reasons for the failure of low-grade motor designs is that the bearings wear quickly. By paying adequate attention to the bearing design while using the highest quality ball bearings, designers can reduce the intensity of the load on the bearings by a factor of 100 plus—optimizing performance and extending life.
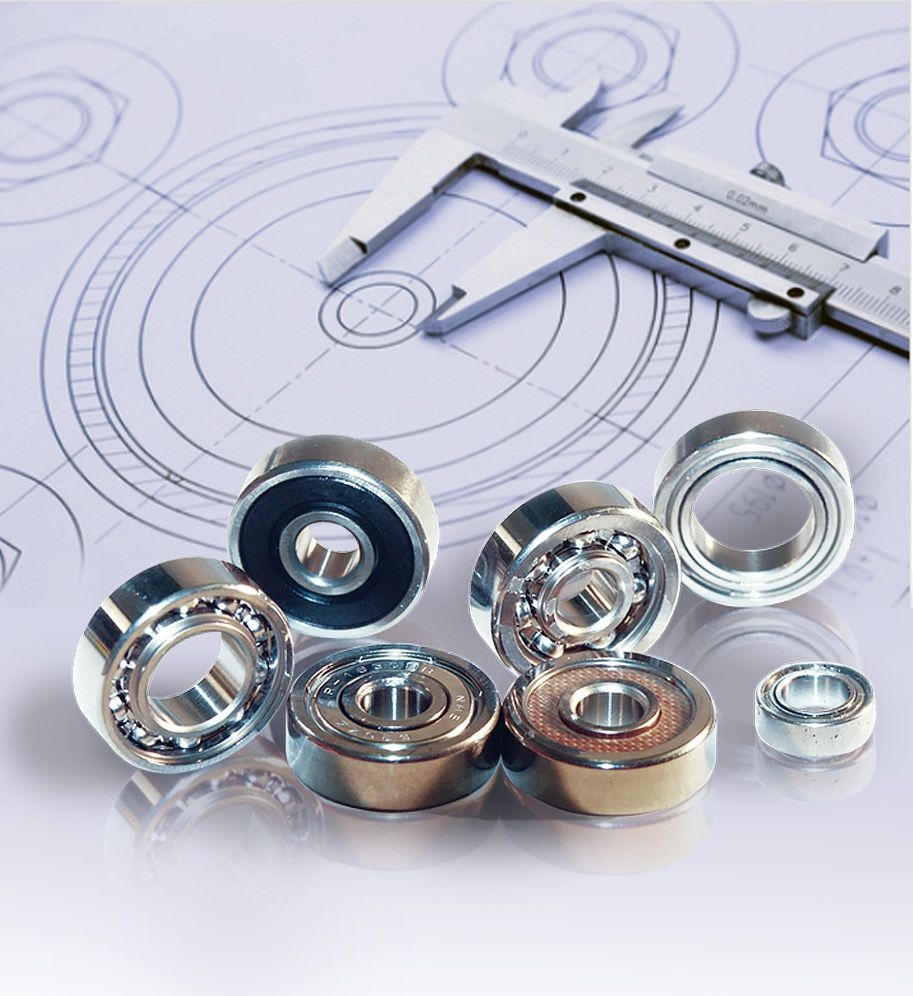
Magnetic Materials
Optimizing the internal balance for a brushless motor can be enhanced through the use of specialized magnetic materials in the rotor that provides higher energy densities within a smaller form factor. Incorporating a neodymium iron boron material means that the rotor assembly can be smaller and provide optimal internal balance for minimal vibration. By getting high energy density characteristics from the material, the designer gets much better performance in a smaller magnet. This also means that the diameter of the rotor can be minimized with a commensurate reduction in inertia, imbalance, and the risk of vibration. Neodymium does not demagnetize over time, either, and therefore provides more consistent performance over a longer period of time than other materials.

Machined Components
One of the key elements in reducing vibration is increasing the accuracy of the components inside the motor. Where typical motors are designed using stamped parts, high-precision brushless DC motors incorporate machined parts. This approach delivers tighter internal tolerances to the motor. In a similar way, high precision motor shafts are straighter and therefore prevent incremental errors from creeping into the motor design. These components can be precision balanced during the manufacture of the motor itself. The internal workings of the motor can be balanced and calibrated to eliminate unacceptable vibration. The motor can then be tested prior to delivery to be sure that the components are properly installed for optimum operation.
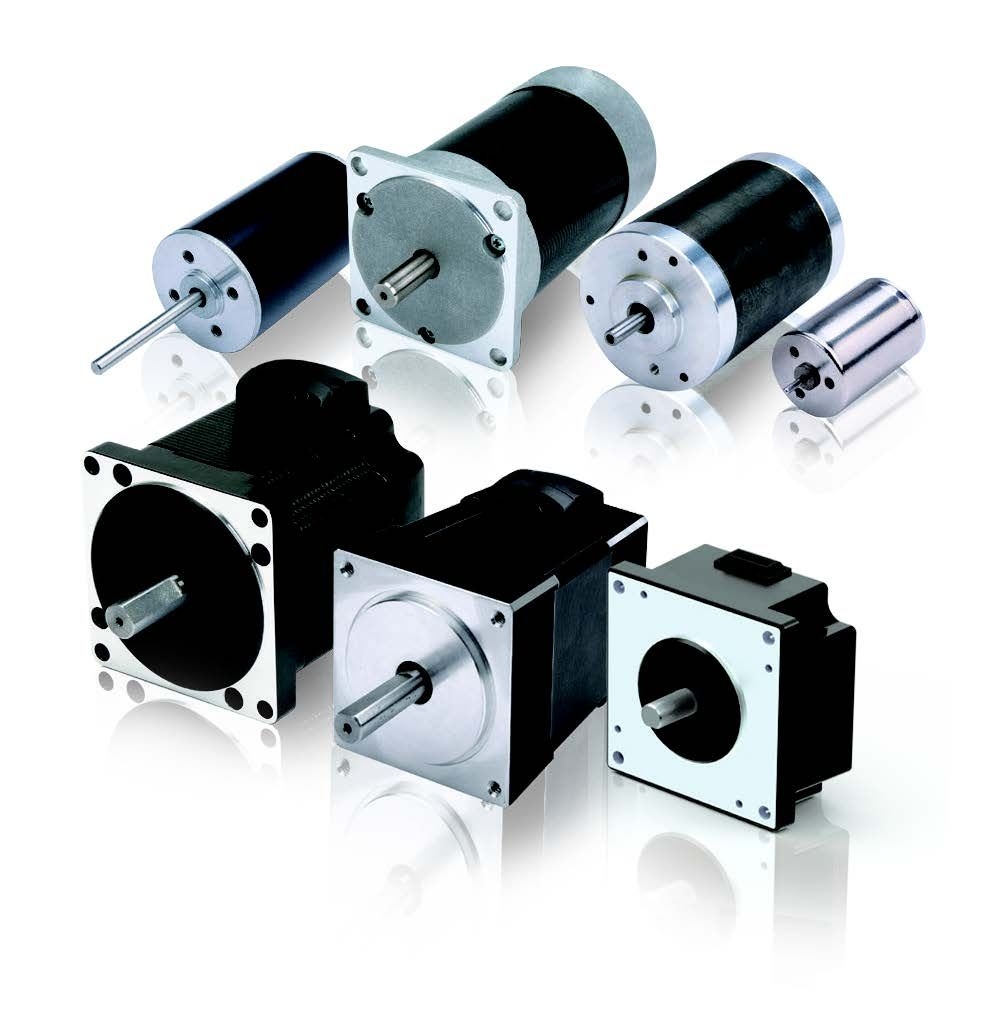
Conclusion
Controlling vibration and noise in a brushless DC motor provides the best possible component for engineers designing a motion solution for their application. A balanced and quiet motor design eliminates many of the factors that can cause high vibration and noise in a system, which reduces performance and can cause early failures through wear and tear. For the high-precision and high-performance applications of today, it is critical that brushless motor technologies deliver low vibration components to users in all industries.
News
Continue Reading
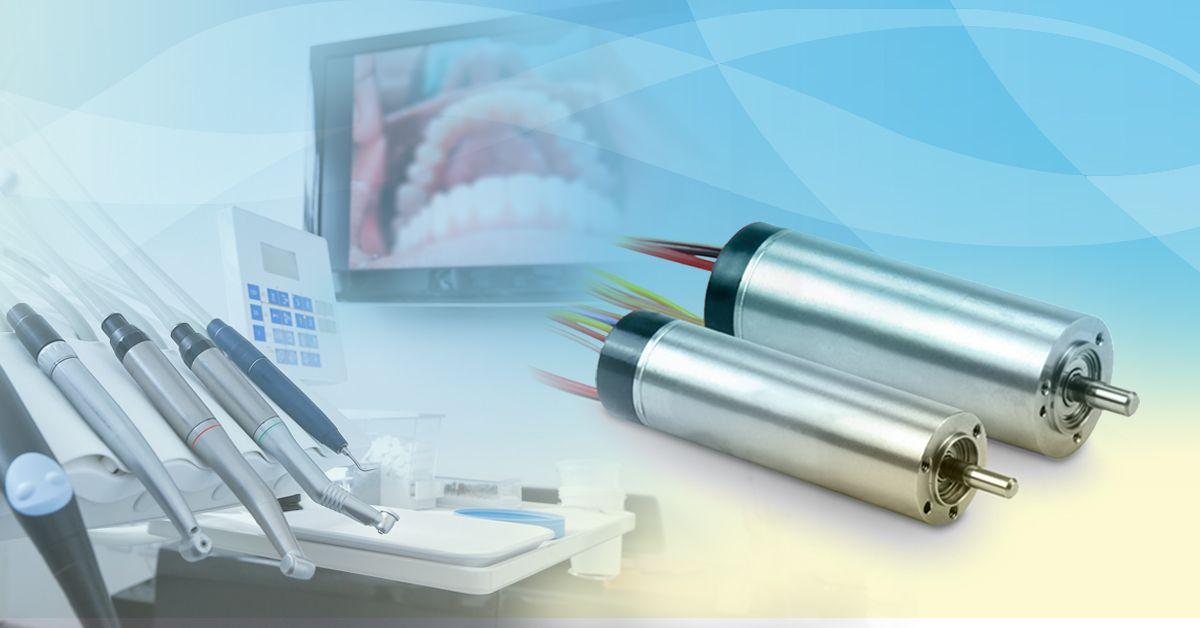
The Advantages of Slotless Motors Over Standard BLDC Motors
Slotless motors have gone through innovations in design as well as manufacturing, making them a good choice for specific applications. This article will explore the benefits and drawbacks of slotless motors and provide information that may help in knowing when to and when not to select them as a solution.
4 Critical Motor Requirements Needed for a LiDAR System
LiDAR is a critical component for driverless vehicles so that they can “see” and react to obstructions that might occur while driving from one place to another. The motor, as a key component to the system, must meet tight application requirements in order to facilitate the requirements of the system.