The Advantages of Slotless Motors Over Standard BLDC Motors
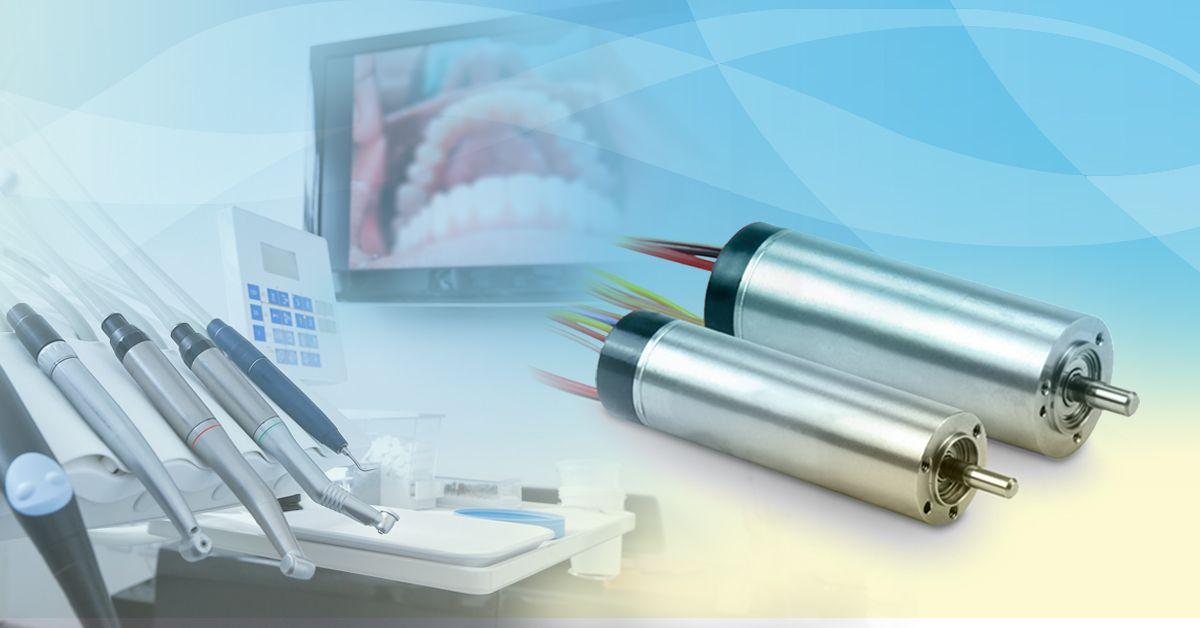
The Advantages of Slotless Motors Over Standard BLDC Motors
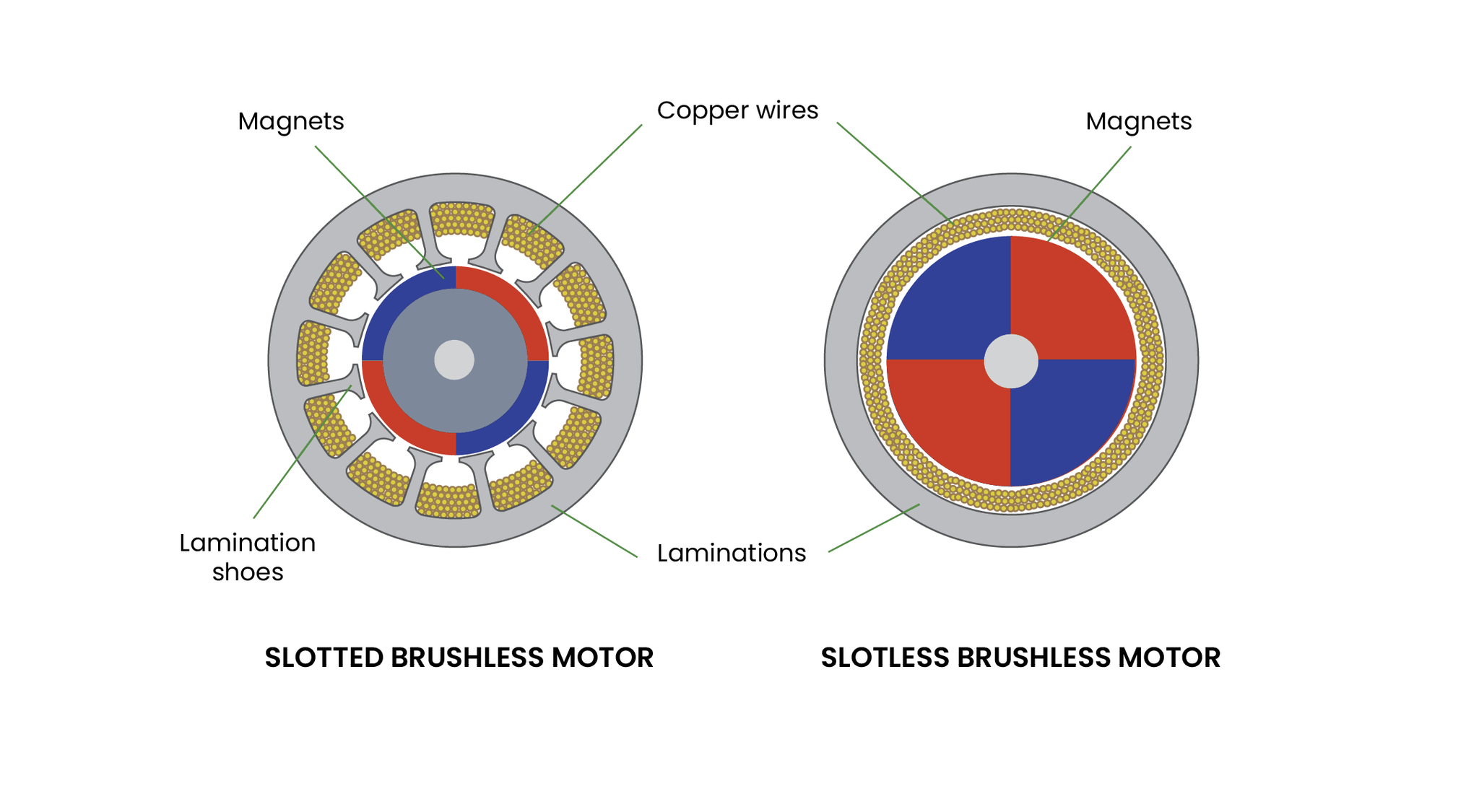
Vibration and Cogging Reductions
Slotted motors are constructed by winding copper wires through slots that are energized to keep the rotor moving. These slots are referred to as teeth. As rotor magnets pass these teeth, there is a greater attraction to the iron at the ends of the teeth than to the air gaps between the teeth, which causes an uneven magnetic pull known as cogging. As a motor slows, the cogging increases as the magnet “snaps” from one iron segment to the next. This motion can also create torque ripple, a loss in efficiency, and vibration and noise.
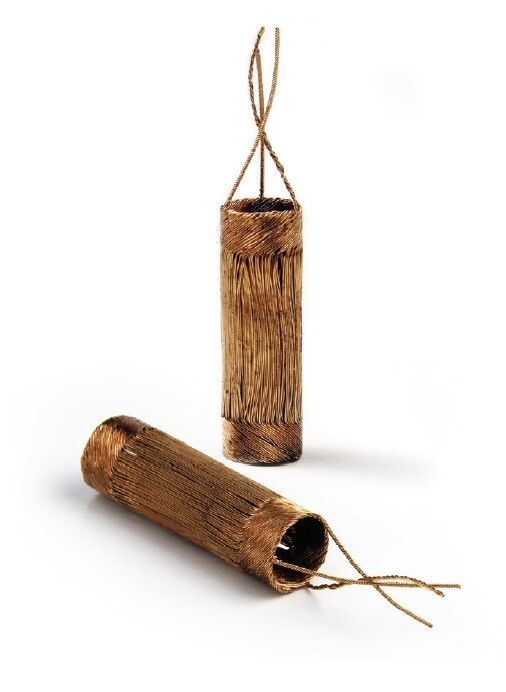
Because a slotless motor eliminates the air gap between iron segments (removal of the stator slot), it produces a continuous back iron geometry thereby eliminating cogging (see Figure 2). A major benefit is smoother running motion at all speeds but most noticeably at slower speeds due to the slotted motor cogging magnification at slow speeds. Any application that required a motor to operate slower than 500 RPM would easily benefit from using a slotless motor.
In addition, the lack of salient poles (protruding iron segments) allows the motor to operate with less susceptibility to saturation (lower peak flux density). With the iron loss reduction, this design enables the motor to operate with a reduction in heat or an increase in operating frequency, since the thermal function of the motor is better balanced.
Further, the torque that is exerted during the detent generated by the slotted motor produces noise in motor operation. By removing the slots, this detent torque is drastically reduced, which greatly reduces the noise output of the motor. Measured noise levels have been proven to be lower than 35 dB.
Medical products and devices are a particular industry where vibration and cogging can be an issue. For precise control in machines that pump fluids into delicate areas such as the eyes, or for use in medical imaging systems, slotless motors are ideal. Another application would be aircraft control systems where smooth feedback control helps a pilot make cockpit decisions. Reduced vibration and noise are also important in handheld production tools as well as scanners, data storage, and other applications where cogging might cause sensitivity problems.
Power, Acceleration, and Speed
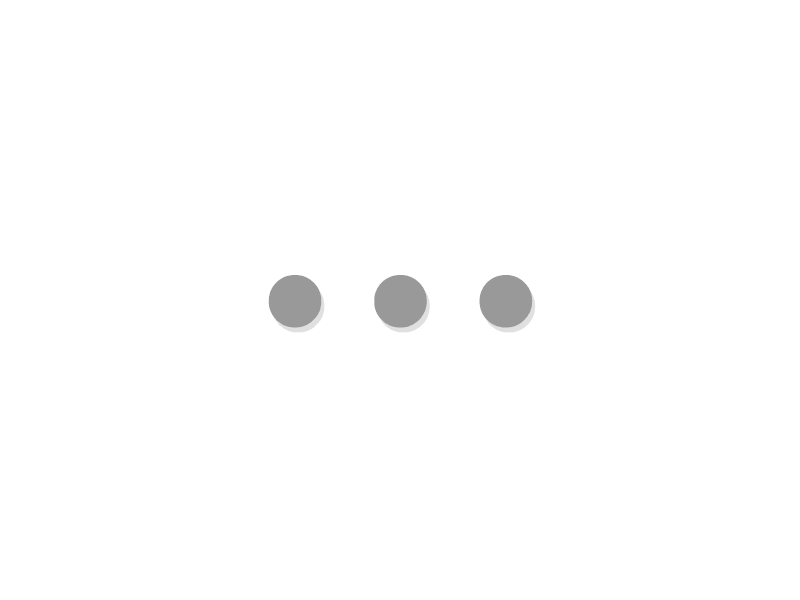
Due to the latest technologies and capabilities of precision tooling and manufacturing, slotless motors have evolved in many ways. While known for generating less audible noise, they were also recognized for providing less electromagnetic interference while allowing for high-speed, fast acceleration capabilities. Designed with sinusoidal torque output that produces negligible distortion (over trapezoidal voltage output), slotless motors were able to reduce torque ripple particularly when also used with a sinusoidal driver (see Figure 4). Because the slotless motor has no stator teeth and no detent torque, it exhibits low magnetic saturation, which allows the motor to operate at several times its rated power for specific intervals of time.
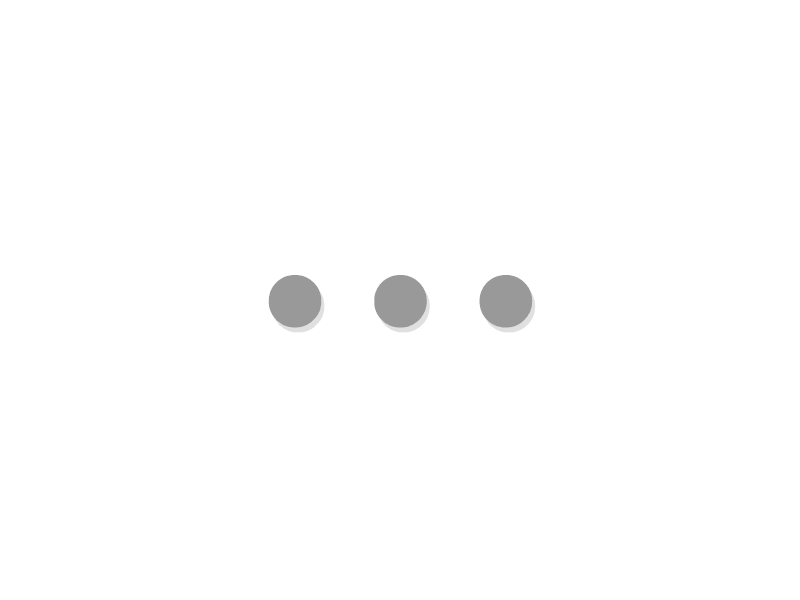
Slotless motor construction has come a long way in terms of delivering power, as well. Through the increased use of high-energy, rare-earth magnets such as samarium cobalt and neodymium iron boron, slotless motors are able to enable the same or greater torque performance than slotted motors. With a focus on using rare-earth magnets and the fewer coils of wire needed for slotless motors to operate, low electrical resistance, low winding inductance, low static friction, and high thermal efficiency are available. This means they run cooler even at high speeds, up to 50,000 rpm.
Modular Design Provides Greater Customization
Companies at the forefront of motor design have taken slotless motor design to its limits. For example, the modular design of slotless motors allows a motor manufacturer to combine their components with the right gearhead to match nearly any specific speed and torque requirements your application may have. Companies such as Lin Engineering offer slotless BLDC (brushless DC) motors with a wide variety of windings so that they can precisely match your specification needs. Motors can also be customized with a variety of sensors, including optical or hall sensors to provide accurate positioning and directional feedback and control velocity.
Getting exactly what your application requires for optimal operation is key. Through unique manufacturing processes, Lin Engineering can build to exacting specifications while remaining cost-effective—due to their modular approach. In addition, motors are built to withstand a minimum of 20,000 hours of continuous (24/7) operation so that users feel confident that their most sensitive applications will operate reliably for a long time.
Modular design means that a wide array of options are available beyond just specification-oriented customer needs. For example, custom connectors and cables can be ordered, shaft modifications such as pulleys and gears can be machined to specifications, and special bearings and windings can be incorporated depending on the application needs.
A Wide Array of Applications
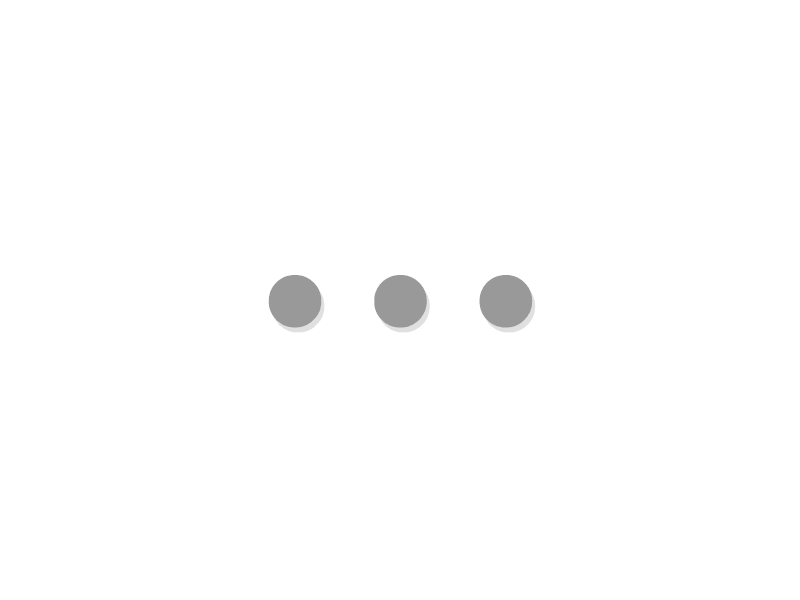
The word of caution when selecting the right motor for your application is to always fully understand the needs of the application. Although slotless motors have come a long way in their design and capabilities, a thorough understanding of your needs is required. As any designer knows, there are too many variables represented in any particular application to even suggest that there is a one-size-fits-all solution. Hence the reason for modularity.
Nonetheless, some applications that would benefit from considering a slotless motor design, include robotic grippers and claws, including those used in medical and surgical tools whether manually or automated (see Figure 5). Slotless motors, as mentioned, are often the ideal choice for miniature pumps and respirators as well as for semiconductor handling equipment and test and measuring equipment, to name a few.
The most encouraging news for customers considering using slotless motors for their applications is that costs continually come down in line with slotted motor costs. This fact is sure to affect how often they are implemented. When cogging is an issue, slotless motors remain the best choice. As technology moves forward, their use will broaden and expand as well.
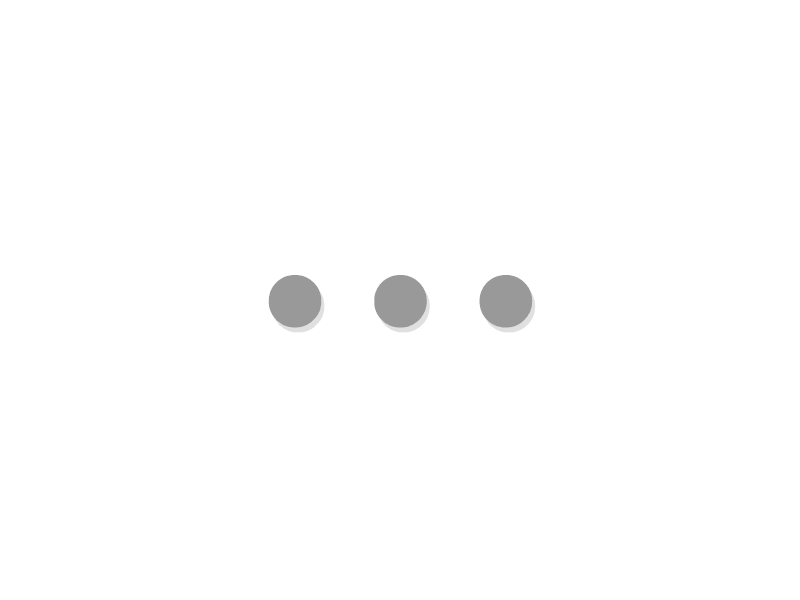
News
Continue Reading
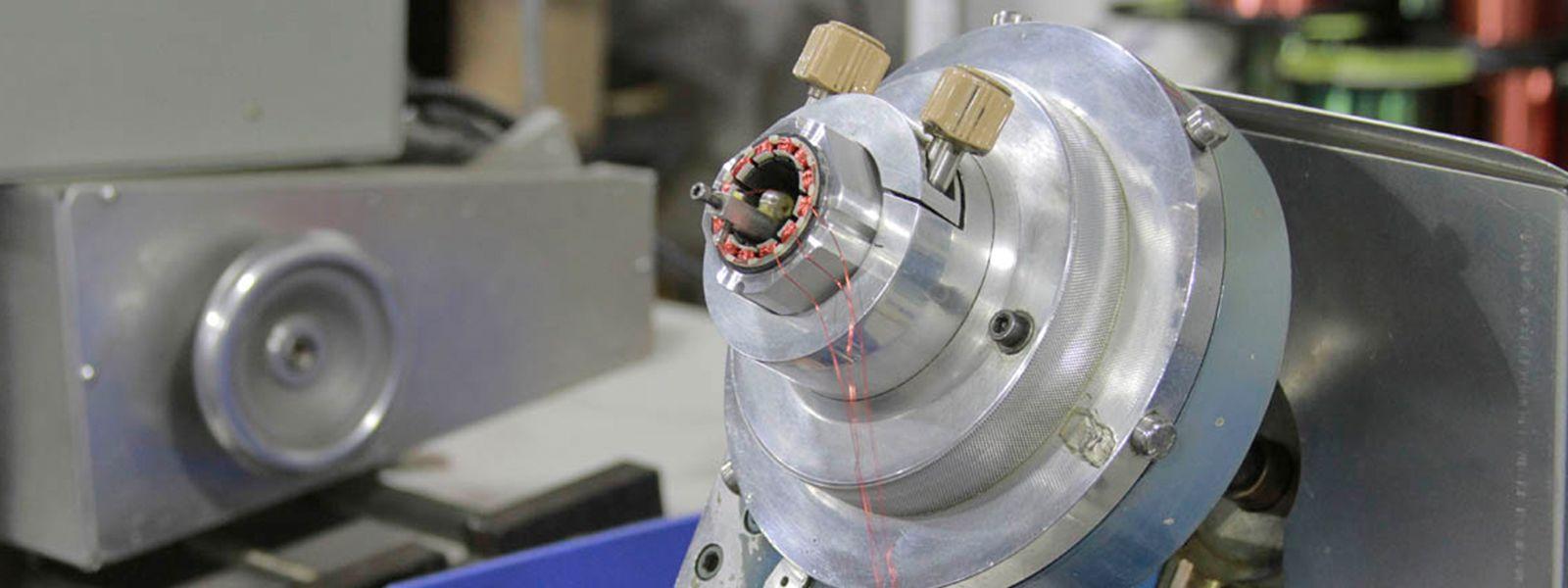
Customize winding of Hybrid Stepper Motors to achieve higher efficiency
There are plenty of modifications we can make to a Hybrid Stepper Motor to optimize the motor’s performance to your specific application, and one of those modifications is customizing the motor’s windings.
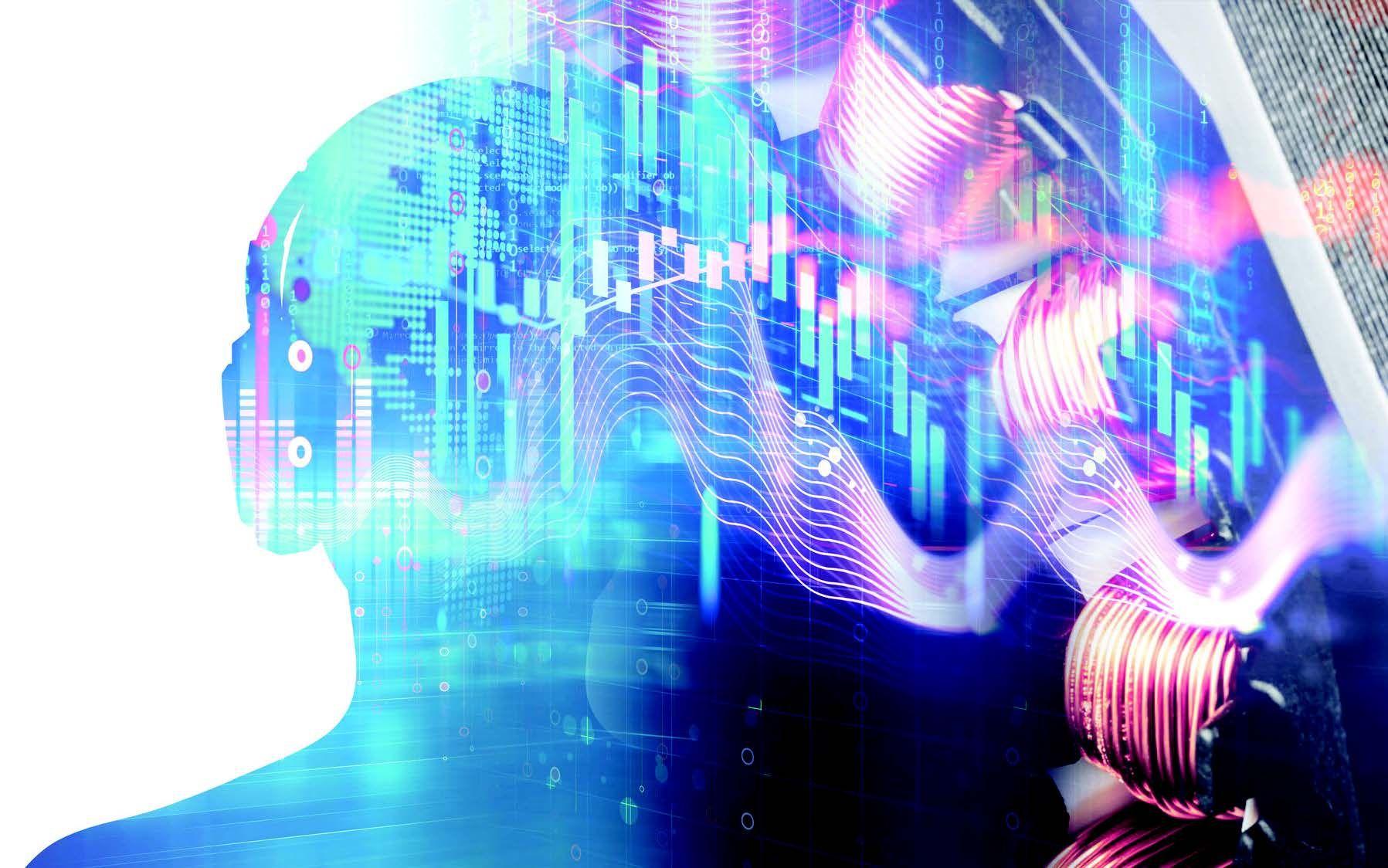
3 Ways to Control Noise and Vibration in a Brushless Motor
Uncontrolled noise and vibration can often cause a system to degrade quickly, affect efficiency, and adversely affect the overall wear and tear of a system. Understanding how to alleviate this problem, when it occurs inside your motor, can increase the life of your whole system.