Multiple Ways to Increase Torque in Your Stepper Motor
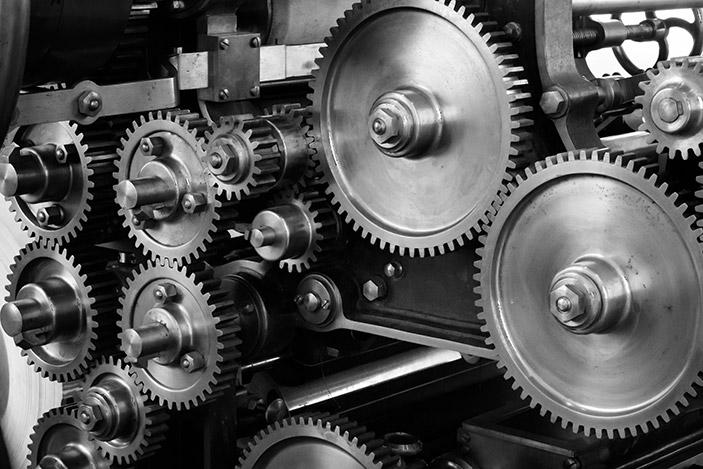
Multiple Ways to Increase Torque in Your Stepper Motor
To increase torque in a stepper motor so that a customer can move greater masses, the first thing most engineers consider is to increase the size of the motor, either via frame size or length, or some combination of the two. When designing for a next-generation product where the footprint and mounting have already been determined, this may not be possible. Here are a few other ways to provide the necessary torque without having to adjust other aspects of the system.
According to Adrian Lucas, Design Engineer at Lin Engineering, “Although one key element might be the main change in motor windings and how we configure them, this is proprietary. We’ve completed years of research on which combinations give us different types of motor performance.” He went on to provide more details by explaining that even though the same winding within the same size motor—both frame and length—will have the same or similar holding torque value, most end users are more concerned with the dynamic torque of the motor. When concerned with dynamic torque, when the motor is moving, a slight change in motor winding will result in different types of motor performance at different speeds.
For example, some windings excel at providing high torque at low-speed ranges, while other adjustments in windings will provide a lower amount of torque at the low-speed range—yet, deliver higher torque at higher speed ranges. Then there are other winding adjustments that provide a good amount of torque at all ranges but require high current output. “As you can see,” Adrian explained, “this is not an easy subject to discuss without some knowledge of all aspects of an application.” To go on, he explained how some windings changes will shift resonance points away from different areas along their torque curve. The result is that the main criteria that changing a winding provides are to vary the operating ranges, change current input requirements, and shift resonance points during operation. Every customer has different needs along these lines and must consider the entire spectrum when adjusting for torque outputs.
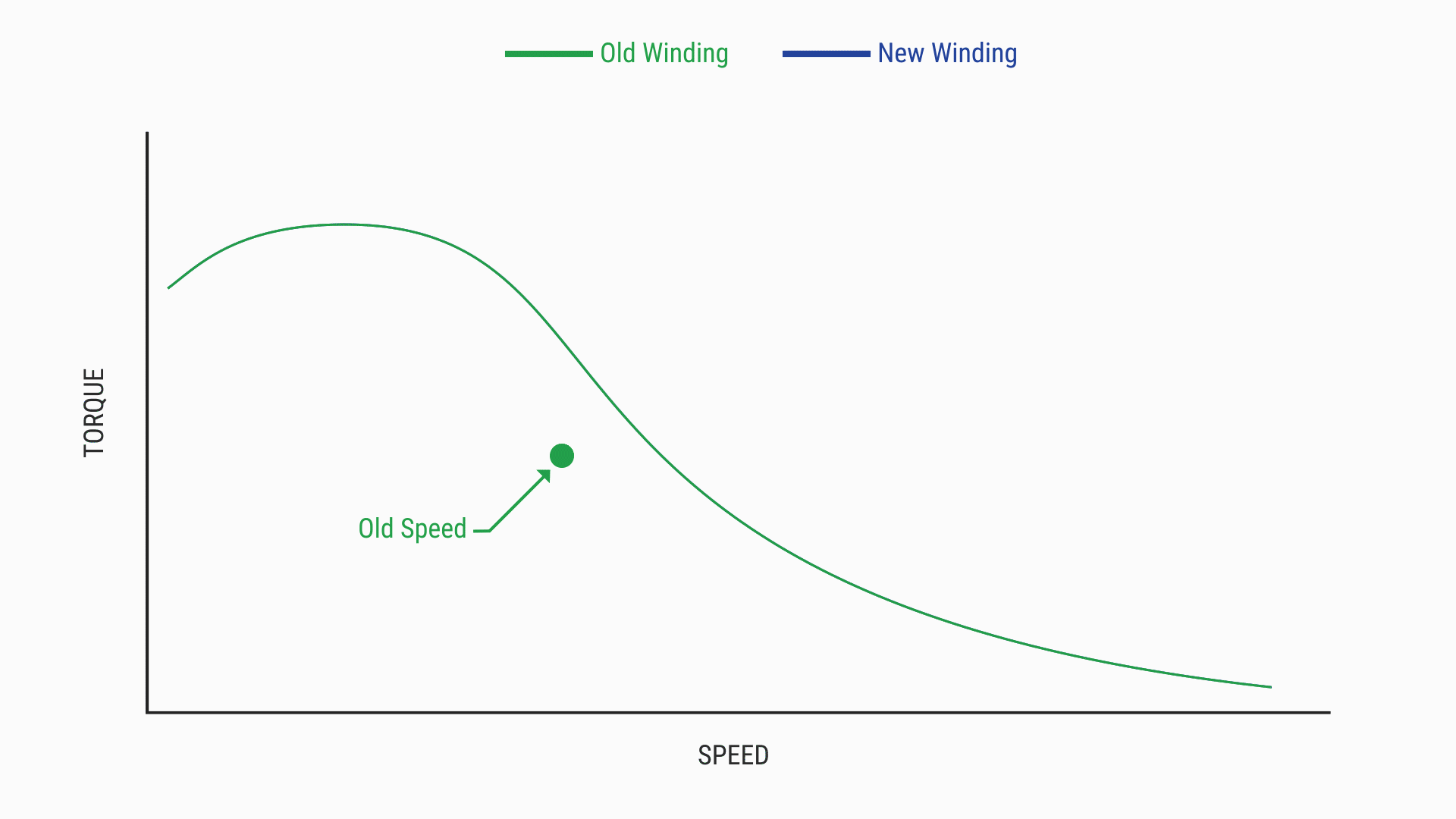
Additional Considerations
To return to the initial place most engineers turn to—if all other specifications allow for it—is that the larger the NEMA size, the larger the torque output, automatically. This is due to the size of the rotor within the motor housing. It’s bigger so it allows more magnetic flux to be generated, resulting in larger rotational forces—torque is greater.
Remember that motors heat up during operation for extended periods of time. Typically, a motor that’s been running for an extended period of time reaches up to approximately 90 degrees C on its own, without considering environmental conditions. Adding a hotter environment would naturally increase the internal temperature to a point that certain internal motor components can begin to fail. This effect can happen inversely when very low temperatures are reached. A variety of internal adjustments may need to be made based on material specification, which is again a necessary evaluation that must be done when providing the right motor. Lin Engineering has solutions that include wire construction, materials used, and some proprietary elements that allow their motors to operate in ambient temperatures as high as 130 degrees C and as low as -70 degrees C for special operations.
Many new users think that if a stepper motor outputs a certain amount of torque that it can do it at any speed. This thinking is incorrect. Torque is highly dependent on operating speed, which must be considered every step of the way for new designs. Typically, the higher your speed, the lower the torque. This relationship though is non-linear. Torque does not lower at the same rate that you increase speed. This ratio can vary greatly from motor to motor and from winding to winding, which is why we covered that aspect first. Once again, there are so many variations that can occur that the best way to understand the relationship of a motor’s torque to speed is to review its Dynamic Torque Curve. These valuable specifications provide engineers with the values needed to illustrate a closer representation of how the motor actually behaves. The curve also changes depending on the type of driver and the way you drive the motor.
The accuracy of the motor is inherent to the physical design of the motor. This is mainly due to the motor’s step angle. The most common step angles are 1.8 Deg and 0.9 Deg motors. The angle references the angular distance it travels for every single step of the motor. This means that 1.8-degree motors are less accurate—but, for this discussion, they provide stronger torque values (and lower speeds) On the other hand, while 0.9-degree motors are more accurate they operate at slightly higher speeds (and provide less torque). Motor accuracy overall, though, will remain roughly the same for both high loads and low loads assuming that these loads are within the rated specification of the motor. The dynamic torque curve for any motor you are considering using is a good indicator if a motor can withstand the loads your application requires. Be aware that when an operating point is close to or above the dynamic torque curve specifications, the step motor may begin to stall or skip steps. This is because the motor essentially cannot generate enough torque to overcome the load.
As mentioned, not only does the speed and torque interactions depend on the type of driver and the method used to drive the motor, accuracy is also highly affected by this same combination. Each driver available acts differently. Although it’s best to consult with the driver experts where you are purchasing them to fully understand the differences, there are some basic concepts to consider. In terms of driving a motor, you are able to “microstep” a motor. Microstepping allows the driver to split each step into multiple steps. A traditional 1.8-degree motor, for example, has 200 steps per 1 revolution. By half-stepping, an engineer essentially generates more steps depending on the way the motor is driven. This allows for users to essentially take only 0.9 degree per step instead of the full 1.8 degree step, resulting in 400 steps per 1 revolution. Of course, when operating the motor in this way the motor will not reflect the same performance as when incorporating a 0.9-degree motor. The lower you choose to microstep a motor, the more inaccurate the motor becomes. “We hear from a lot of engineers who want to microstep the motor and have to explain that when you take a 1.8-degree motor and microstep it, you may be only moving 0.9 degrees, but step accuracy lowers by a large margin.” This can be perfect for some applications. For example, the best application for microstepping typically comes in removing resonance in a system as well as smoothing out motion profiles of a motor to achieve certain speeds in a faster or slower amount of time.
Companies that provide options for custom and semi-custom motor designs to meet specific needs must be able to provide final designs that also meet your pricing requirements. This is why companies like Lin Engineering have developed, in-house, modular construction methods that allow them to provide rapid prototypes for evaluation and then to put into production—typically in volume—the exact motor needed for an application. This flexibility allows the company to meet the short lead times of the design stages as well as the high production volumes of the manufacturing stage of an application.
As you can see, there are a lot of ways to adjust torque specifications in a motor, all of which have a cascading effect on other specifications and, ultimately, on general operations. Considering your entire application profile means that you can better select when a motor needs to be adjusted for your specific needs.
Speak with one of our motion control experts about your next project.
News
Continue Reading
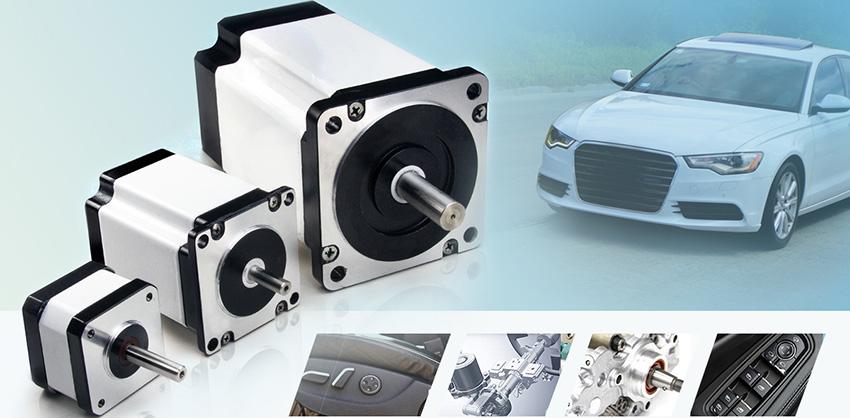
Stepper Motors in Automotive
Fulfilling the needs of the automotive industry with motors that can be used on the road, off-road, or on the racetrack, engineers expect quality and long-life. For applications from automobile air conditioning systems, fuel and injection pumps, power-assisted steering, window control, and power seats, motors must operate precisely and reliably even under the most demanding environmental conditions.
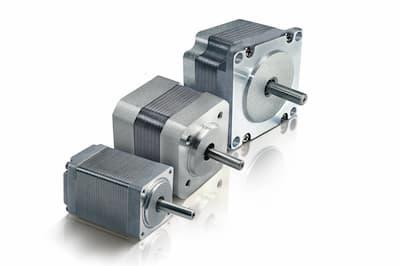
Load Calculations and Tips for Using Stepper Motors
Making sure your motor is the proper size for your equipment needs is key to ensuring long life, performance, reliability, and cost for your application. Below, we’re going to consider load calculations as well as provide a few tips in applying this information to step motors.