Solutions First: Solving Problems with Electric Motors
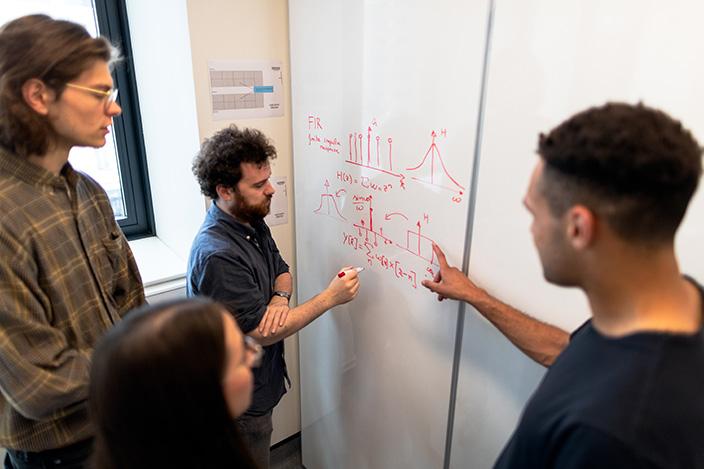
Solutions First: Solving Problems with Electric Motors
It may not be totally visible just yet, but there is a shift in the way companies are approaching the engineering development of new equipment and systems. At one time, a design engineering team consisted of several types of engineers who were experts in their fields. These teams would meet and go over the characteristics of an innovation or new system based on customer research, and then decide how to approach the job from the most logical positions—each person from his or her own experience and expertise. This approach has evolved over the last ten or more years.
Consultants and engineering service businesses grew to a point where engineering in certain vertical niches was being outsourced. This has grown since certain vertical experiences are no longer an in-house commodity, particularly for motion applications. We are not only talking about finding the right product that will move an object from one place to another, not simply about the torque and speed of a motor, but about mounting structures, space allotment, noise, vibration, component materials, windings, and much more. These decisions need to be made specifically for the project you are tackling.
This is particularly the case where product operation is critical to health, safety, or where failures are very expensive. Such applications go through certification processes, either through governmental agencies like FDA or FAA, or private certifications like space flight worthiness. Once designed in it is difficult to replace such components without going through the certification process all over again. These applications are most likely found in air and spacecraft, medical and lab automation, and autonomous vehicles.
When an engineer is developing a piece of equipment or a system for one of these industries, one that is meant to be manufactured in volume, one that requires motorized motion control, they don’t need a product so much as they need a solution.
Challenges to Innovation and Creativity
Overlapping performance in motor types provides one of the major challenges for engineers. For example, you can find similar specifications for stepper, servo, and brushless DC motors. When considering the same type of motor, such as a stepper, the choice of serial versus parallel operation can be an issue in certain applications, as are winding specifications. These challenges appear to be solvable from a variety of directions until the application is looked into more deeply where some specific problems appear not to have a solution at all. For example, finding a motor that conforms to a certain size or form factor and delivers the right amount of torque at a required speed, along with an acceptable amount of resonance, noise, and heat generation may look impossible, forcing many engineers into selecting something that is close—either over-engineering or under-engineering depending on the pressures of time or budgets.
Optimal performance often requires choosing the right winding paired with the right bearings, couplings, leads, and connectors, etc. that will integrate with the system they are being designed into. All this adds to the chances that an engineer could easily select the wrong motor for the job, use a motor that is not optimized for their specific application, or one that is improperly integrated with their system. All of the above-mentioned challenges are tackled every day by design engineers who consider the product their top priority. But there’s another way to approach this challenge.
The Solutions Approach
In the solutions approach to innovation and creation, there are three basic elements: find, optimize, and integrate. This may sound simple, but when you consider all the options that are available combined there are literally millions of different ways to go. Finding is key in getting started. Like a target, finding incorporates everything around it—all those concerns mentioned in the preceding paragraphs. Knowing your application and its environment from the start of a project to its end will help you to “get close” to selecting the right product. This is where most design engineers stop and continue straight on to purchasing. Our aim here is to remind engineers that purchasing a product is not the same as purchasing a solution.
Once you’ve gotten close, it’s time to call in the experts. What we’re talking about are the engineers working for a particular motor manufacturer, ones who know their motors inside and out, and can help optimize your motor for the specifics of your application. It’s often the case that once an engineer determines those key characteristics that are necessary, they still might select the wrong type of motor for their project. Although a stepper or a servo motor might be able to fit some similar specifications, they do not offer the same overall characteristics an application might need. Optimization includes tightening up on the requirements to the extent that you are looking at what windings will work, what magnets, what bearings or sealing technologies. Optimization means getting exactly what will work for you.
It’s time to step back from your research now that you’ve gotten to a solid choice so that you can focus on how to customize the motor for seamless integration. Customizations at this point could easily include framed or frameless motors, sealing choices, bearing choices, and interconnection methods. Now is the time to consider whether you’ll be operating in an open-loop configuration or need to go to a closed-loop configuration, at which time you’ll want to know what type of feedback will most effectively perform as you need.
Ongoing Support Structures
Throughout this process, you’ll need to be sure you’ve had the proper engineering support as mentioned earlier. If your in-house expertise is focused on other issues, engineering support for your motion system will be even more important. Where many companies have salespeople ready to take your call, you’ll want to be sure you work with another engineer instead. Following up with engineering help is the more relevant from an experienced engineer at your motor manufacturer’s location, one who knows how to analyze every application challenge you may run into.
Prototyping support is essential at this point. To be sure that the motor you ordered will operate as planned, a test prototype will provide assurance, particularly if you’re looking to order a large volume of product. The prototype should come from the manufacturer of the motor you will eventually choose so that you can feel confident that the specifications and characteristics will be maintained. Be sure you can get the motors quickly, as well. This will all help with maintaining cost-effectiveness overall. Finally, be sure that you’ll have supply chain support that guarantees on-time scheduled delivery that will fully support your own manufacturing process throughout the lifecycle of your project.
Conclusion
When you are looking for a solution instead of merely a product, it is best to go to the experts, typically as close as the manufacturer of the motors themselves. Search out the company that has solved multiple complex motion problems before, and that can help you to optimize and customize a product that fits your specific application. Be sure that they will not only deliver a quality prototype but can manufacture in quantity when you need it, and provides the supply chain support that guarantees product availability.
News
Continue Reading
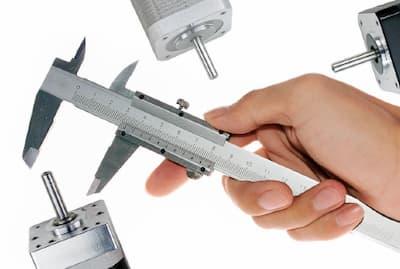
How Does Quality Distinguish Itself in a Step Motor
On the surface step motors across different manufacturers often look similar to one another. From the outside, this is very much the case, but inside—as everyone can imagine–quality becomes more apparent. But quality isn’t just something you design into a step motor.
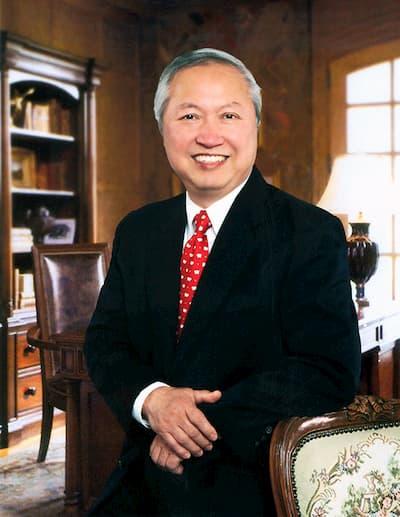
It’s Not Just About Motors - Ted Lin's Story
Ted Lin’s story isn’t the usual tale about starting out in a garage and building a product that everyone wants. Well, it is that story, but with a few twists along the way. Maybe what’s more important is how he grew up.