How Does Quality Distinguish Itself in a Step Motor
How Does Quality Distinguish Itself in a Step Motor
Quality is bandied about so often that it has become a cliché. Even if it’s being used as a buzzword, so many engineers brush the idea away before looking more deeply into the situation. Every company wants to use the word, but how many live it? At Lin Engineering, quality is an attitude, it’s a way of life. Easy to say but, in this case, it’s also something that can be described at every step of the design. Quality, first and foremost, must be taken seriously from the top down.
Driven by the president executive staff of the company, Lin Engineering has gone to extreme lengths to devise its own internal quality control system. They call it the 4.5 Sigma Way because six sigma was not a satisfactory method for what they wanted users to experience from their products. The company felt that only through rigorous quality control could they assure that customers got exactly what they needed—not just what would work—for their application. Through this system, they felt confident that customers would get “A motor that performs up to the specific requirements, consistently, and reliably for the life of the motor.” This goal is especially critical in high-volume production, where an entire assembly line can easily grind to a halt because of a product defect. Not to mention costly RMAs. To ensure the quality of the company’s step motors, they focus on three critical areas where quality matters on a monumental level: component quality, design quality, and manufacturing quality.
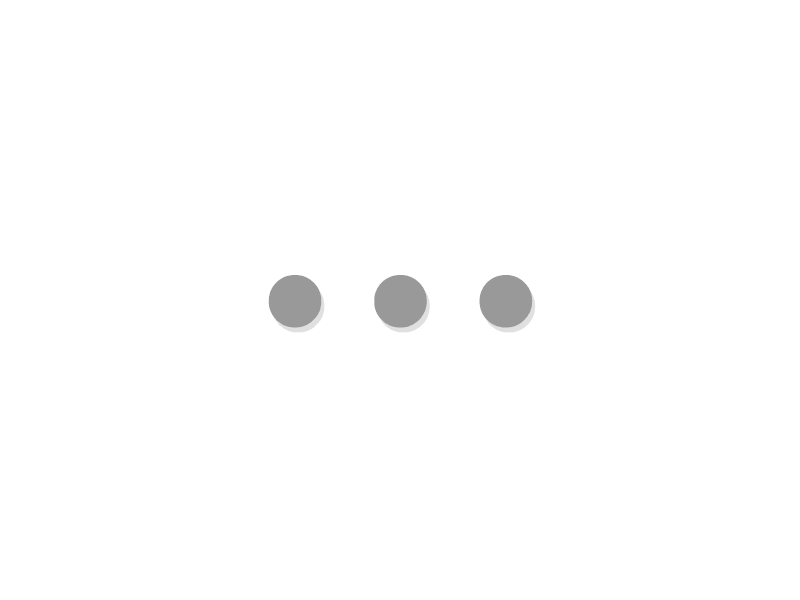
Quality Components
When considering the quality of components, it’s important to note that there are multiple sub-assemblies involved in making a step motor: stator, rotor, shafts, bearings, end caps, windings, leads, connectors, etc. Further, each of these sub-assemblies can be divided into sub-components, such as wire, insulation, housings and seals, connectors, and the materials these items are made out of. No one will be surprised when we suggest that the quality of each component matters. From the bottom up, every component must be of the highest quality in order for the final product to carry that through.
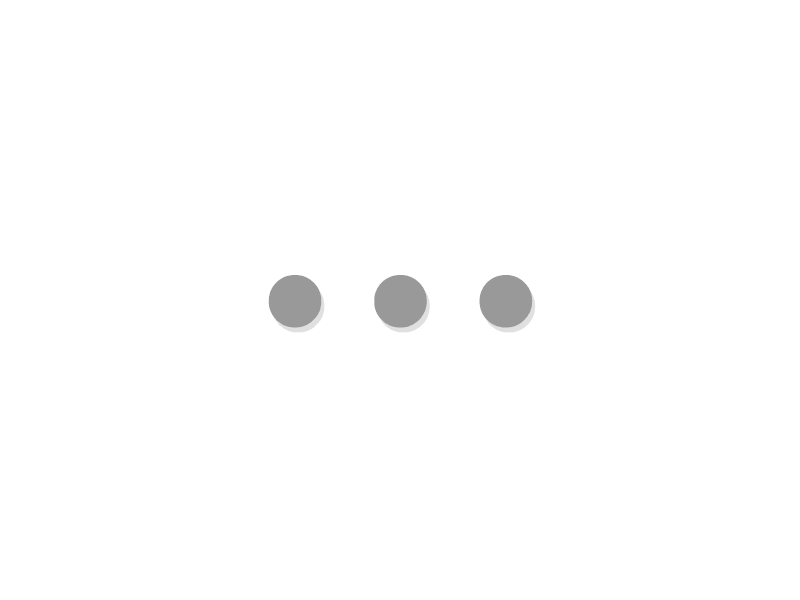
When it comes to a step motor, dimensional accuracy and concentricity of the rotor, stator, and end caps are especially important. It’s important to maximize the magnetic flux passage over the stator and rotor teeth while minimizing the magnetic reluctance. To do this, the air gap, or space between, the rotor and stator need to be minimal. The smaller the air gap, the less room for error in component construction. This sounds easy enough to understand, but if the concentricity of either, or both, components is poor, the result in an uneven air gap will cause erratic performance. In a worst-case scenario, where contact occurs, the motor will be rendered useless.
Some manufacturers remedy this inconsistent concentricity by increasing the size of the air gap between the rotor and stator, reducing the possibility of them making contact. This is effective only in eliminating failure. This approach significantly hinders the performance of the step motor, where the greater the variations between components the more inconsistent the performance becomes. Even slight variations have huge effects on inertia, resistance, inductance, dynamic torque output, and resonance (unwanted vibration).
Other critical components include the end caps, which hold the bearings in place and ensure proper alignment between the stator and rotor. The bearings themselves also need to be of the highest quality in order to maintain and assure the longevity of the step motor.
Each pole is essentially an electromagnet, which makes it important that each pole is wound consistently using the highest-grade wire available. Variation in the diameter of the wire can cause issues with the consistency of the winding for each pole. This would result in poor torque specifications, would increase resonance or vibration, and produce poor resolution in the end product. This is why at Lin Engineering every component is fully scrutinized through their 4.5 Sigma Way. They rely on every team member to catch even the slightest variation and to address the issue long before it moves on to the next stage.
Design Quality
Working our way up to the design aspects of the final step motor product, let’s look at some basic design criteria that the company uses to maintain a quality product. The obvious design factors—such as 1.8 degree/step motor design or 0.9 degree/step motor design—are very important, but there are many other critical elements to consider. As mentioned, the relationship between the stator and rotor plays an enormous role in the performance of the motor: the air gap, alignment of the teeth between two components, and the placement of the magnets. But what about each sub-system? Let’s take them one at a time. The rotor design is critical to maximizing the performance of the motor. The rotor must display an adequate magnetic surface while remaining as light as possible to minimize the rotor’s inertia.
Rotor inertia affects the total performance of a step motor. A low inertia rotor is able to respond faster and can deliver higher speeds and higher dynamic torque to the user. Proper end cap design assures maximum internal volume to insert a large rotor. End caps are responsible for the proper alignment of the rotor. Misalignment, as mentioned, can have a large effect on the quality of the final product. An out of alignment rotor leads to an uneven air gap and causes erratic performance.
Through understanding what a customer might want, Lin Engineering is able to help design in the right components. The stator, for example, can be adjusted based on what the end goal of the design is required to deliver: high precision, smoothness, or high torque output. The design of the poles determines how much winding material can fit between the stator poles. Plus, the number of poles—commonly 8, 12, or 16—correlates with the accuracy and torque output of the motor. Shafts need to be strong enough to withstand the repeated torque loads and axial forces without deforming or degrading over time. Similarly, bearings have to match the performance and life expectancy of the final product. As the one component that often determines the life of the motor, the bearings often experience the most wear.
Manufacturing Quality
Often customers consider the design of a product without remembering that the manufacturing of that product is just as key to its quality. If each component, each assembly, and each final step motor is not put together perfectly, every time, all that quality control of the components, sub-assemblies, and design can be discarded. Inconsistencies in the assembly process can often cause the exact same issues and inconsistencies as those noted in the component section of this article—even if the components are all of the highest quality. Plus, it is one thing to manufacture a motor that meets a required specification, but an entirely other issue when you need to manufacture 100,000 motors with consistency and reliability.
Through the use of Lin Engineering’s mean value control system—the 4.5 Sigma Way—every motor that leaves the facility must meet that control figure. To be sure this is true, every motor is tested to meet the required electrical specifications (resistance, inductance, leakage current), torque specifications (holding and detent torque), mechanical specifications (front shaft extension dimension and overall body length), and any other special feature specified by the customer. The company goal of assuring that the motor delivered to the customer has the precise specifications that the customer requires is maintained on a daily basis. This gives customers the confidence that the step motors will perform consistently and reliably with the application.
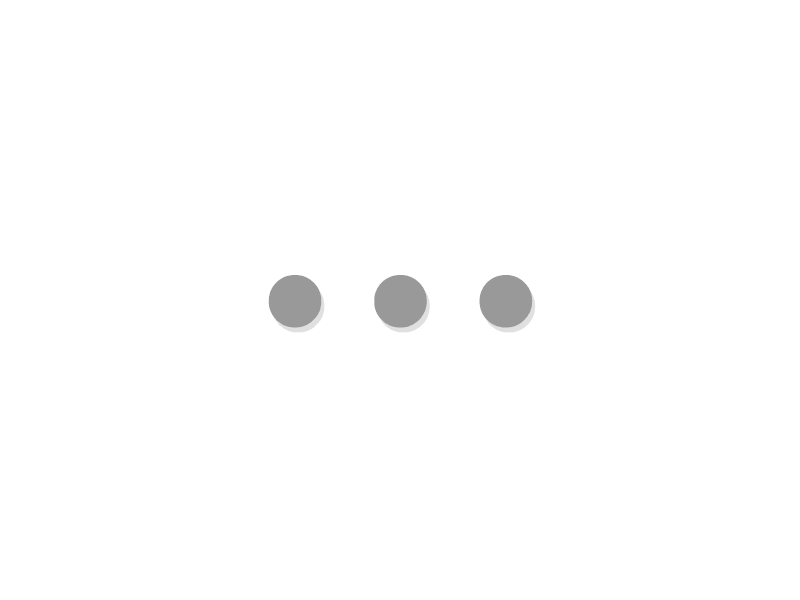
Further, the company follows ISO9001 standards, as well as assemble their motors in accordance with the most rigorous AS9100 standards—the standard used to assure flight safety for aeronautics and space applications. As a company, Lin Engineering has thirty years of design experience. The company’s engineers have reinvented the step motor from the ground up, contributing to the amazing growth of the industry to where it is today.
News
Continue Reading
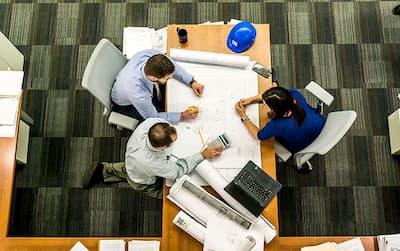
Motor Product Manufacturer, Engineering Consultant, or Both
Motor technology is getting more complex and more nuanced than ever before. This trend has made it extremely difficult for engineers to understand exactly what they may need for a particular application.
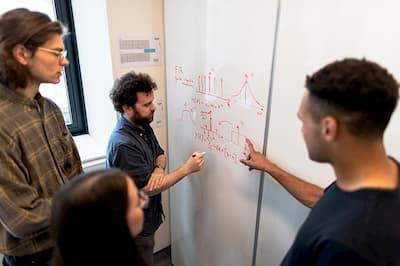
Solutions First: Solving Problems with Electric Motors
How some companies are approaching the shift away from in-house engineering expertise to make working with manufacturers more palatable for new product development, product iteration changes, and innovation—particularly in the motion industry.