Request a Quote
ZH417 SeriesZH417-11-03Hybrid Stepper Motor
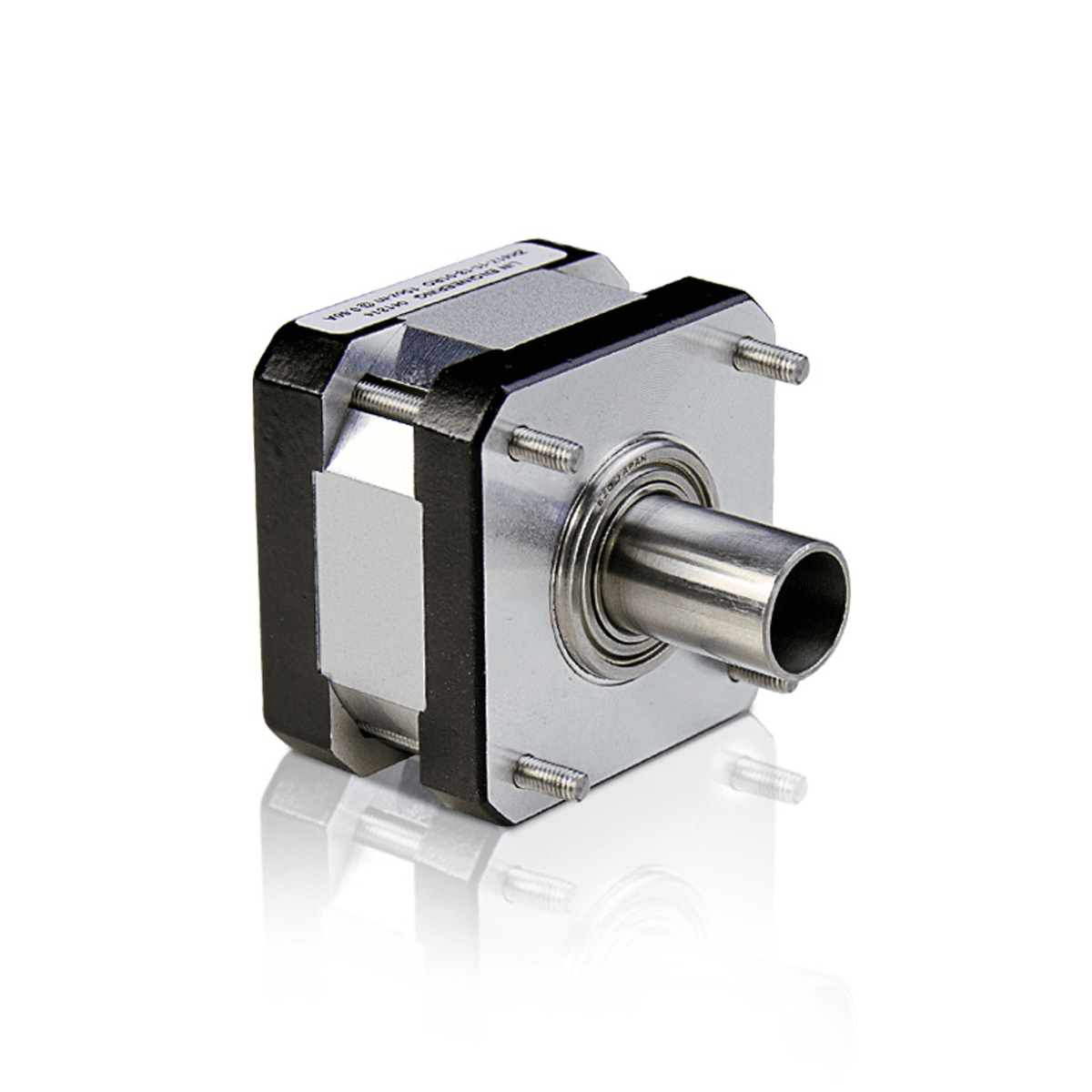
Quick Facts
ZH417-11-03 Hybrid Stepper Motors
- NEMA 17 (1.650 in) Frame Size
- 0.9° Step Angle
- 1.100 in Length
- 16.99 oz-in Holding Torque
- Signature Series Technology for ultimate smooth motion and high accuracy
- Large Hollow Shaft Design
- High Step Accuracy
- Virtually Zero Detent Torque
Dimensions
Model | DIM. A (length) in MAX |
---|---|
ZH417-11-03 | 1.100 in |
Torque Curves
Speed
Find the motor that fits your Target Torque (oz-in) and Target Speed (RPM)
Motor Specifications
Base Motor Part Number | ZH417-11-03 |
Step Angle | 0.9° |
Frame Size | 1.650 in |
NEMA Size | NEMA 17 |
Body Length | 1.100 in |
Current (AMP) | 1.2 AMP |
Holding Torque | 16.99 oz-in |
Resistance | 2.85 ohm |
Rotor Inertia | 0.12 oz-in² |
Number of leads | 4 |
Connection | bipolar |
Weight | 0.351 lbs |
Operating Specifications
Radial Play | 0.001 in @ 1 lbs |
End Play | 0.003 in @ 3 lbs |
Shaft Run Out | 0.002 TIR |
Concentricity of Mounting Pilot to Shaft | 0.003 TIR |
Perpendicularity of Mounting Pilot to Face | 0.003 TIR |
Max Radial Load at Dimension "K" from mounting face | 6 lbs |
Dimension "K" | 0.620 in |
Max Axial Load | 6 lbs |
Maximum Case Temperature | 176.00 °F maximum |
Ambient Temperature | -4 °F to 122.00 °F |
Storage Temperature | -4 °F to 212.00 °F |
Humidity Range (%) | 85% or less, non-condensing |
Magnet Wire Insulation | Class B 130 deg C |
Insulation Resistance | 100M Ohm at 500 VDC |
Dielectric Strength | 500 VDC for 1 min |
Features & Benefits
We've Reinvented the Step Motor
Conventional hybrid stepper motor utilizes a permanent magnet in the rotor. Our patented design uses a ring magnet in the stator instead. This drastically reduces the detent torque (unenergized drag torque) because the magnetic flux path is able to reach over the stator windings and go through only the outer edge of the rotor. Reducing detent torque improves accuracy, smooth operation and reduces noise. Best of all, modifying the magnet location does not change the dynamic torque.
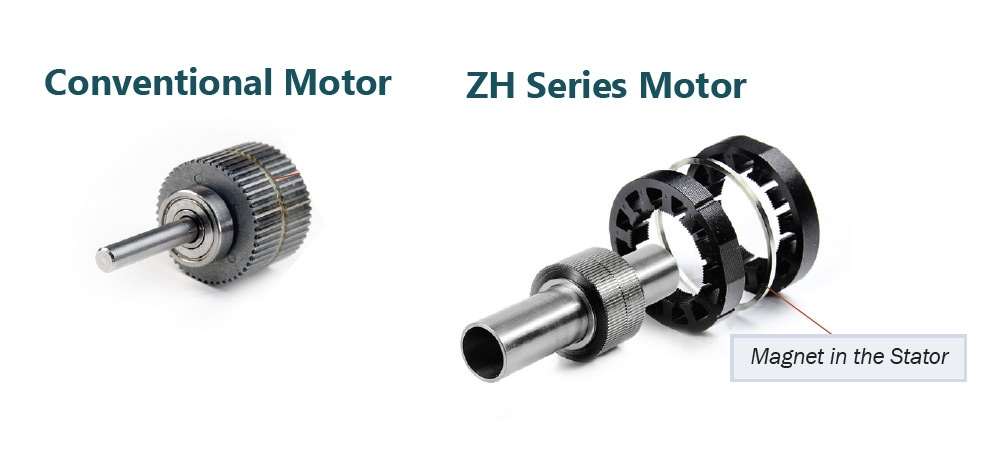
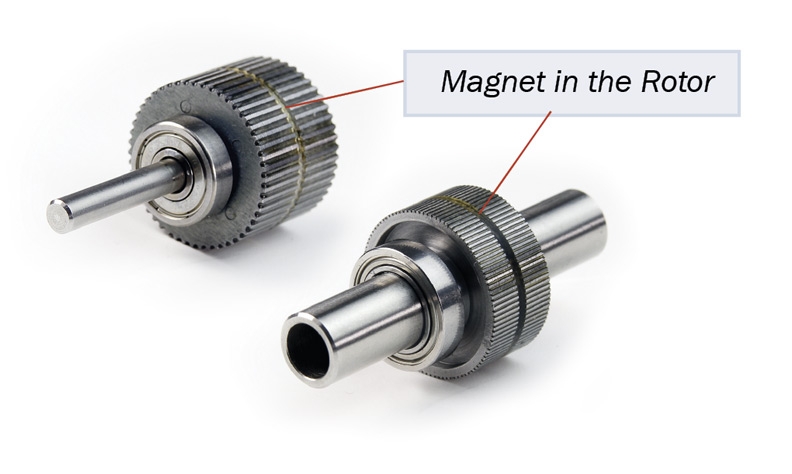
Large Holow Shaft Up to 11 mm in Diameter
Conventional stepper motors cannot accommodate large diameter hollow shafts without sacrificing torque and performance. Torque is dependent on the size of the magnet placed in the rotor. A large diameter shaft reduces space available for the magnet, thus sacrificing torque.
Since we’ve moved the magnet from the rotor into the stator stack, we can accommodate a large shaft without sacrificing torque or performance.
Extreme accuracy
Z-Series motor maintains ±1.5 arc minutes error under 64x microstepping. Industry average can range from ±4.5 to ±18 arc minutes in 0.9° step motors.
Quiet Operation
By eliminating detent torque, the motor operates substantially quieter than regular hybrid stepper motor.
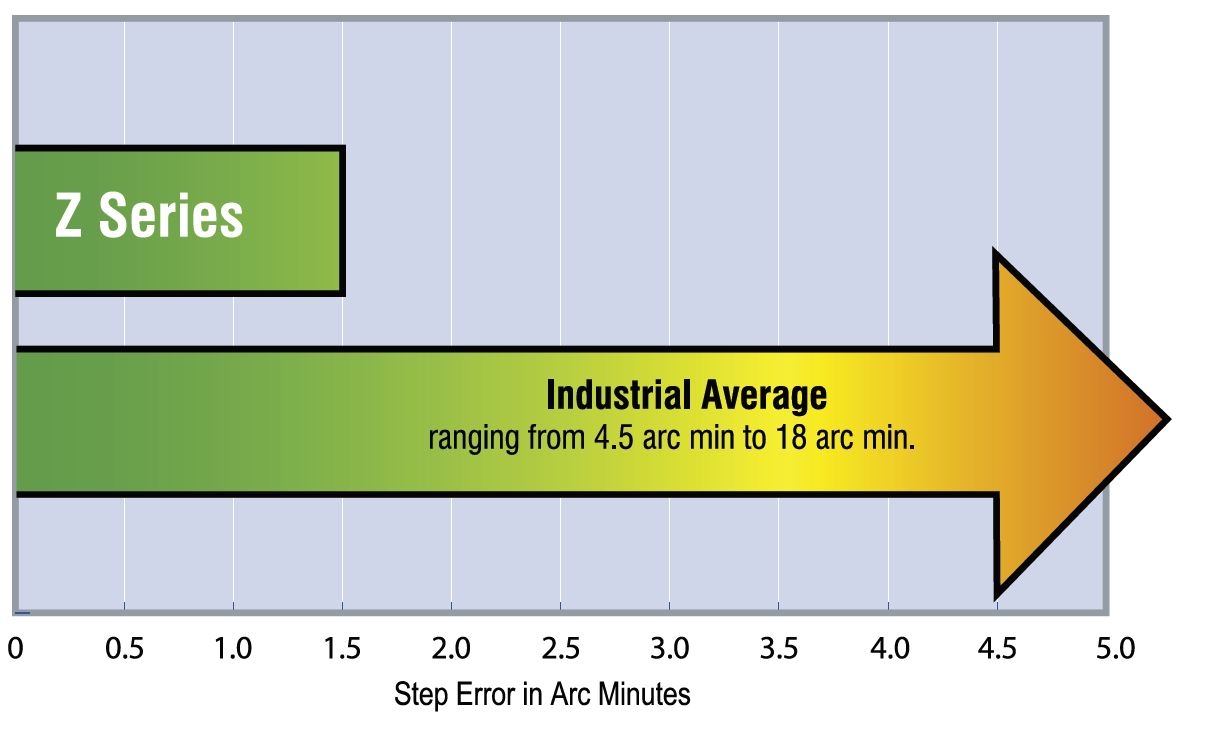
Video Overview
Customizations & Optimizations
Lin Engineering can ensure that your hybrid stepper motor is optimized to deliver the required performance for your specific application, whether it’s increasing torque at a specific speed range, reducing noise or vibration, or optimizing for minimal power consumption, or making specific modification to ensure proper and native fit within your assembly.
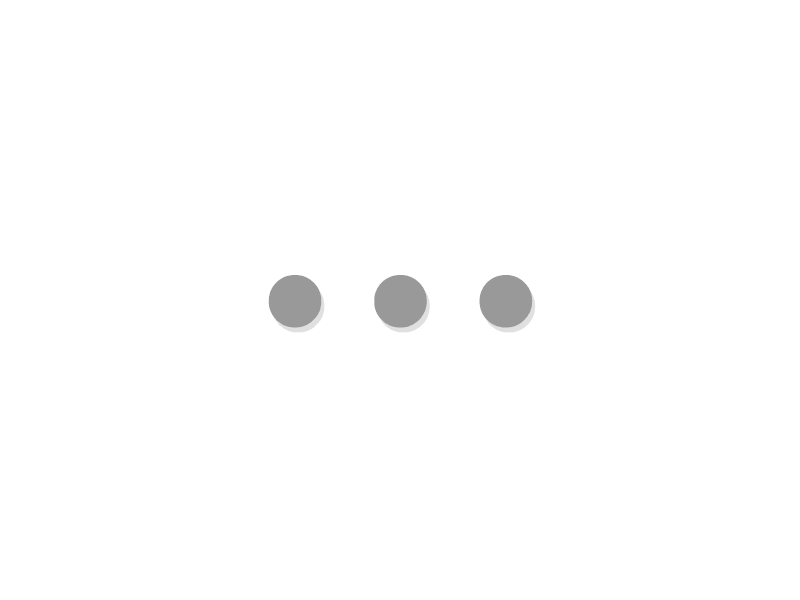
Customization Services Include:
- Optimized Winding
- Multiple Shaft Options
- Customized Leads & Connectors
- Customized Housings & Mountings
- Bearings & Lubricants
- Mechatronic Solutions
- Environmental Protection
- Drivers & Controllers, Encoders, Gearboxes & Accessories
The result is that you’ll get a motor that is fully optimized for your specific applications and configured to seamlessly fit with your assembly. This reduces your product's complexity, and increases the speed and ease of the assembly of your final product.
Speak with one of our sales representatives about your specific application needs by filling out a request for a quote.
ZH417 Series
Related Products
Downloads
Get the motor you need
Just fill out a Request for a Quote form, and tell us about your application and your needs. One of our applications specialists will review your request, and provide you with a quote promptly.