Advantages of Servo BLDC Motors in Automated Guided Vehicles
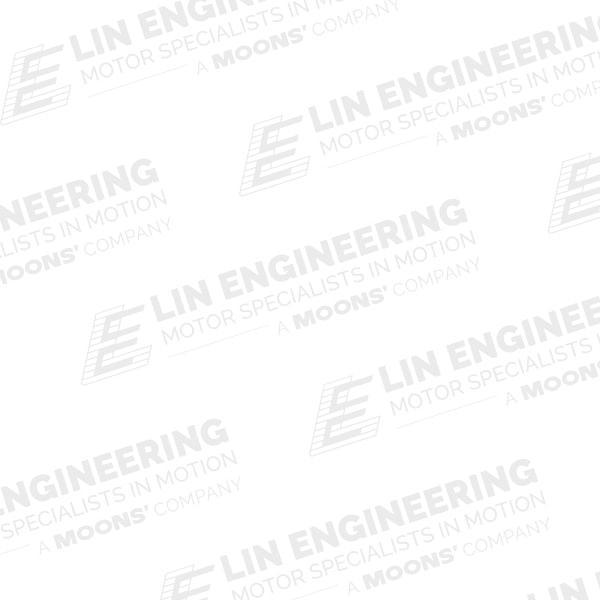
Advantages of Servo BLDC Motors in Automated Guided Vehicles
As early as the 1950’s, Autonomous Guided Vehicles have been helping automate and speed up processes. At first, AGVs utilized wire or tape on the floor to guide them along as they completed their tasks. Although such technology is still used today, AGVs have come a long way since their early days. Autonomous Guided Vehicles have become much more complex and capable. Today’s robots can sense their environment to automatically navigate their way through it. They can communicate with each other to perform certain tasks in tandem, as well as work safely among people. The AGVs form factor is also diversifying rapidly. Depending on the job at hand, autonomous robots and vehicles can come in a variety of shapes and sizes—from skateboard-sized robots moving light objects, to large fork-lift-sized robots moving or towing heavy machinery. But despite its size or shape, a robot may seem simple on the outside, however, the inside is filled with complex sensors and electronics, and of course, a large assortment of DC motors to provide the required motion. The most obvious application for DC motors is to perform the task of driving and steering the robot so let us take a closer look at how and what motor works for this job.
One of the biggest benefits of an autonomous vehicle or robot is that it can move around on its own. This allows it to transport goods from one location to the next by following a complex set of instructions. In other words, precise position control is critical. Engineers often reach for DC servo motors to drive AGVs as servos deliver the precise speed and position control required for the application. But what are servo motors? “Servo” is a very loose term used to describe a closed-loop motor system: one that most often consists of a motor, a position feedback device such as an encoder, and a driver/controller that can process the feedback from the motor in real-time and adjust the motor’s operation based on the feedback (see figure 1).
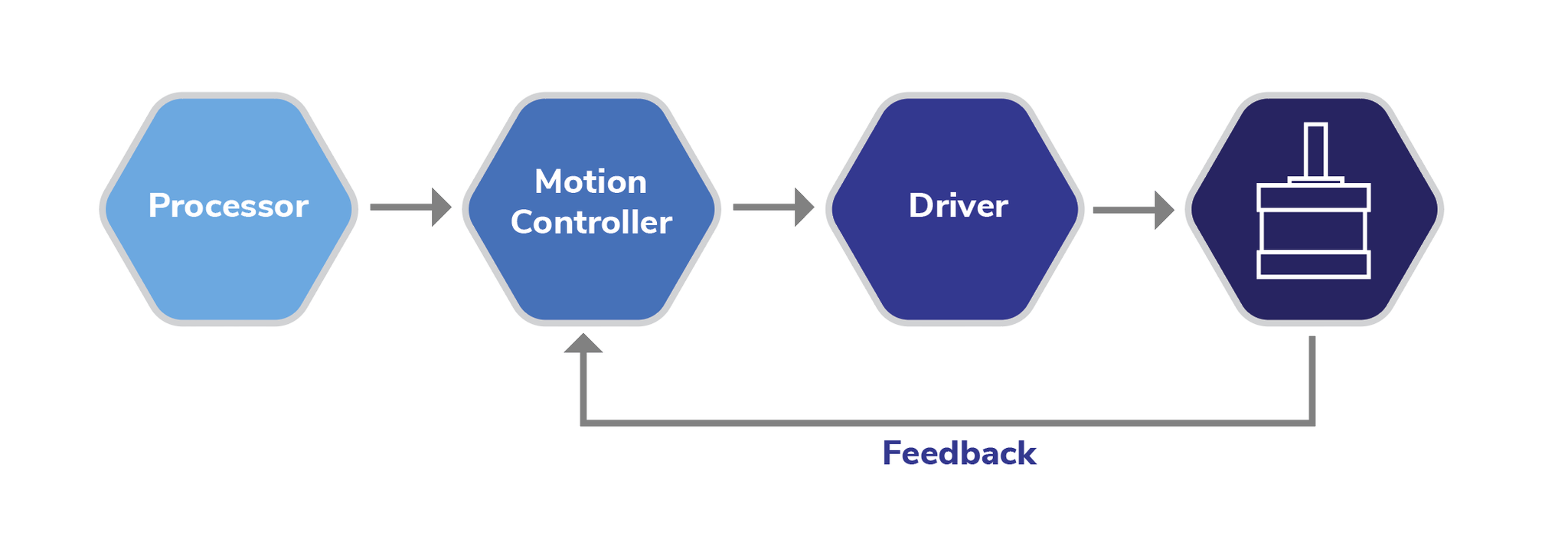
Servo motors can come in many different types, shapes, and sizes. For instance, a 300mm BLDC hub motor with a corresponding feedback device and controller/driver can be considered a servo motor, and so can a NEMA 11 hybrid stepper motor with a similar setup. These two motor types seem like polar opposites of each other, but they can still be classified as Servos. Therefore, the term “servo” does not necessarily describe any particular motor type, but rather a type of system.
On one hand, having a large variety of motor types to choose from allows for greater engineering flexibility, but on the other hand, narrowing down the exact motor type best suited for the application can be a daunting task. To choose the right motor, engineers need to consider specific constraints of the AGV device they are designing. Constraints such as loads the AGV will be subjected to, its operating speed, acceleration and deceleration requirements, type of power supply used (is it a “wired” or a battery-operated system?), available voltage and amperage in the system, operating temperatures, environment, shape and size of the system, the list goes on. This does not even account for non-mechanical requirements such as budgetary needs. It may be tempting to design an array of high-performance motors with high-precision gearboxes, mechanical brakes, high-resolution encoders, and high bit-rate controllers with the newest communication protocols, but for certain applications, this type of solution can quickly raise the price tag of the final unit beyond what the market will bear. In those situations, engineers need to be creative.
The largest and most obvious constraint in the AGV drive system is the minimum amount of torque at the speed needed to propel the AGV forward. Lightweight robots may have more choices in this situation than their heavier counterparts. For instance, lightweight AGVs may be able to utilize a simple hybrid stepper motor for the drive motor. In this case, a fully closed-loop system may not even be required since the position of a hybrid stepper motor can be accurately controlled without a position feedback device, making such systems extremely economical. For larger robots, however, engineers may choose more traditional brushless DC motors to drive the units. BLDC motors tend to provide more torque, especially at higher speeds, than hybrid steppers can. BLDC motors can also provide smoother and quieter motion, but to achieve accurate position control, a position feedback device is needed. Therefore, AGVs that utilize BLDC motors for the primary drive mechanisms almost always use servo systems.
A direct drive system without a gearbox or drive reduction mechanism is the simplest and most cost-effective solution, however, a direct drive system is not always possible or practical. A motor may prove to be too large or too heavy to be used in the application. Generally, engineers want to reduce the footprint of their devices as much as possible, therefore the motor should also shrink with the size of the vehicle. On other occasions, an application can be size-constrained and a motor with maximum allowable envelope may be unable to deliver the required amount of torque for the application. One way to remedy this situation is to add a gearbox to a motor to multiply its torque output. Motors can be paired with gearboxes of various gear ratios. Commonly torque can be increased by a factor of 10, 20, 50, or more, with the caveat that speed is decreased by the same factor. But often engineers can hit the right balance of torque at speed using a properly sized gearbox/motor combo while reducing the size and weight of the system compared to direct drive configurations. Hitting specific torque at speed targets is only a part of the challenge.
Mobility is the key feature of AGVs. While some AGVs are externally powered, being tethered to a power supply is often not an option. For this reason, many AGV systems are battery-powered. However, reliance on battery power can create a couple of roadblocks for engineers. For one, the overall system is often power constrained, which means there is a limited amount of voltage or amperage available to operate the motor. And two, the system needs to be optimized for the best battery efficiency to minimize the power drawn by the motor. Closed-loop systems are highly efficient by design since power input can be modulated to provide only as much power as needed to perform the task, but a closed-loop system is often only a part of the solution. A fully optimized motor is the other part.
Off-the-shelf motors are usually designed for a broad range of performance, which is great for general applications or for prototyping purposes, but this does not translate for optimal efficiency within any specific application. Most applications operate within specific speeds and torque ranges. If these target ranges are known, then the motor's winding can be optimized in a variety of ways to ensure optimal performance within those specific ranges and within the power input constraints.
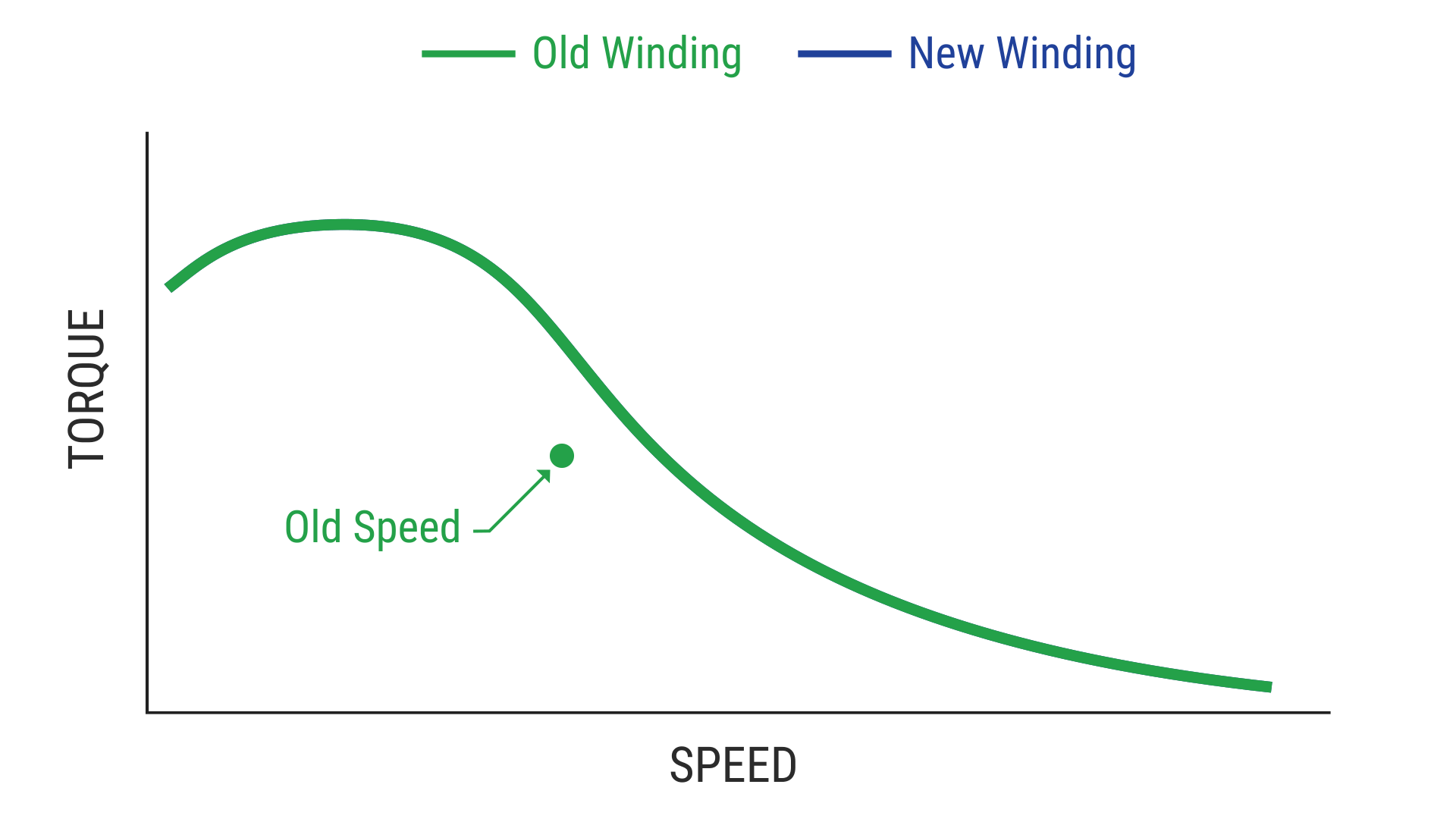
When winding the stator, there are many variables that will affect the performance characteristics of the motor. Things like the gauge of the wire, the thickness of the wire insulation, the number of turns per coil, the tension of the magnet wire, along with other things will impact the motor’s performance characteristics. The exact winding recipe will affect the amount of current that can be applied to the motor, the rate of charge and discharge per pole, the strengths of the magnetic flux, and more. This is why we can have many motors of the same stack length, using the same stator and rotor components, but with large variations in performance. Winding dictates the amount of torque and speed the motor can achieve.
The benefit of fully optimized motors for battery-operated devices is that they will draw less power than off-the-shelf motors at those specific speed/torque targets. A lower power draw means extended operation on a single charge or allows engineers to reduce the battery pack size (and overall system size and cost) while retaining performance.
Whether you are building an autonomous guided vehicle or an autonomous mobile robot, Lin Engineering is your one-stop shop for custom motors. We make a variety of custom motors including hybrid stepper, BLDC, frameless, slotless, and more. Our team of engineers will help find an appropriate motor for your application. They then optimize the motor for the best performance within your specific application. Lastly, the motor and its housing are customized to ensure it seamlessly integrates into your application.
News
Continue Reading
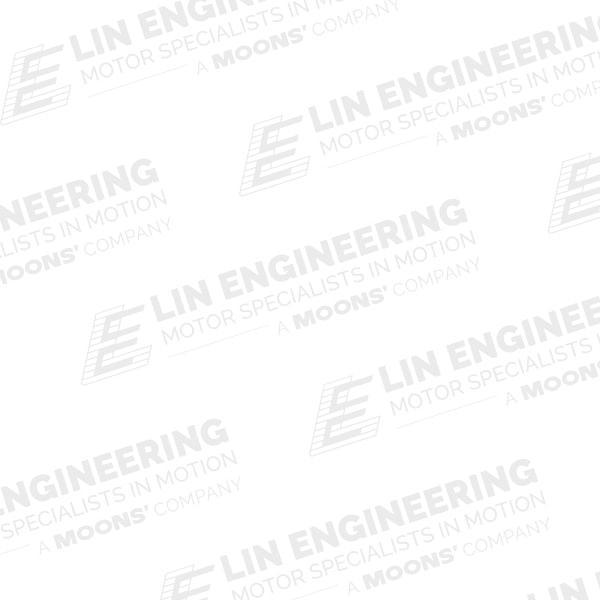
Utilizing Frameless BLDC Motors for Electromagnetic Resistance in Next Generation of Smart Home Gym Equipment
The new generation of smart home gym equipment utilizes BLDC motors such as our frameless motors to provide electromagnetic resistance. Such gym equipment often needs to be as light and compact as possible while still offering a full and complete workout. Frameless motors are ideal for this application because they eliminate wasted space and redundancy by design.
Foam Densifier Reduces Lin Engineering's Environmental Footprint
Lin Engineering uses a Foam Densifier to recycle foam and to help reduce our environmental footprint. This machine has helped reduce our overall waste by up to 75%.